Thickeners
Thickeners are a type of industrial equipment used for separating solids from liquid in a wide range of applications, such as densifying product for efficient processing, countercurrent decantation (CCD) washing, clarifying wastewater streams, and tailings management in mining and aggregate processing applications. Depending on the application, the valuable product can be the clarified liquid or the thickened solids.
How Diefenbach Thickeners Work
Diefenbach thickeners are comprised of a tank, feed pipe feedwell, rake (and pickets, depending on the thickener style), a bridge containing the rake drive mechanism, and a chemical dosing system.
The slurry feed enters the thickener from a de-aeration tank and into the feedwell. Chemicals are added to the feed to aid in rapid settling of the solid particles in the slurry. These chemicals can be flocculants or coagulants, depending on the application. They attract the fine solids in the slurry to form larger, heavier particles that sink to the bottom of the tank.
As the flocculated solids settle to the bottom of the tank, the rotating rake mechanism assists with moving them toward the discharge cone in the center. The thickened solids are then discharged out the bottom of the tank and, depending on the application, sent to waste or further processing.
The solids-free liquid (or liquor) overflows the weir surrounding the top of the tank. Again depending on the application, this clarified liquid is then sent for further processing or reuse as process liquid.
Why Diefenbach Thickeners
Diefenbach thickeners are designed based on decades of knowledge and experience with liquid-solid separation. Diefenbach's thickeners are designed based on computational fluid dynamics (CFD) modeling and material testing in Diefenbach's in-house lab. With features such as the company's innovative feedwell, which allows for the optimum distribution of flocculated solids throughout the tank, Diefenbach thickeners achieve the ideal liquid-solid separation for a wide range applications, including CCD washing and tailings management.
As part of the McLanahan Family of Companies, Diefenbach thickeners leverage decades of experience and hundreds of installations.
Features & Benefits of Diefenbach Thickeners
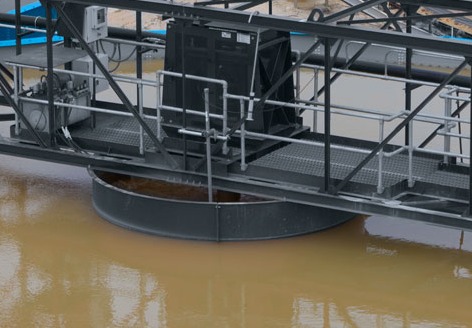
Advanced modern feedwell and auto-dilution options
State-of-the-art feedwell designs allows Diefenbach thickeners to achieve maximum density underflow with reduced needs for polymers.
Auto-dilution options further increase the rate of settling of particles to reduce the size of equipment required and maximize thickener clarity and underflow density.
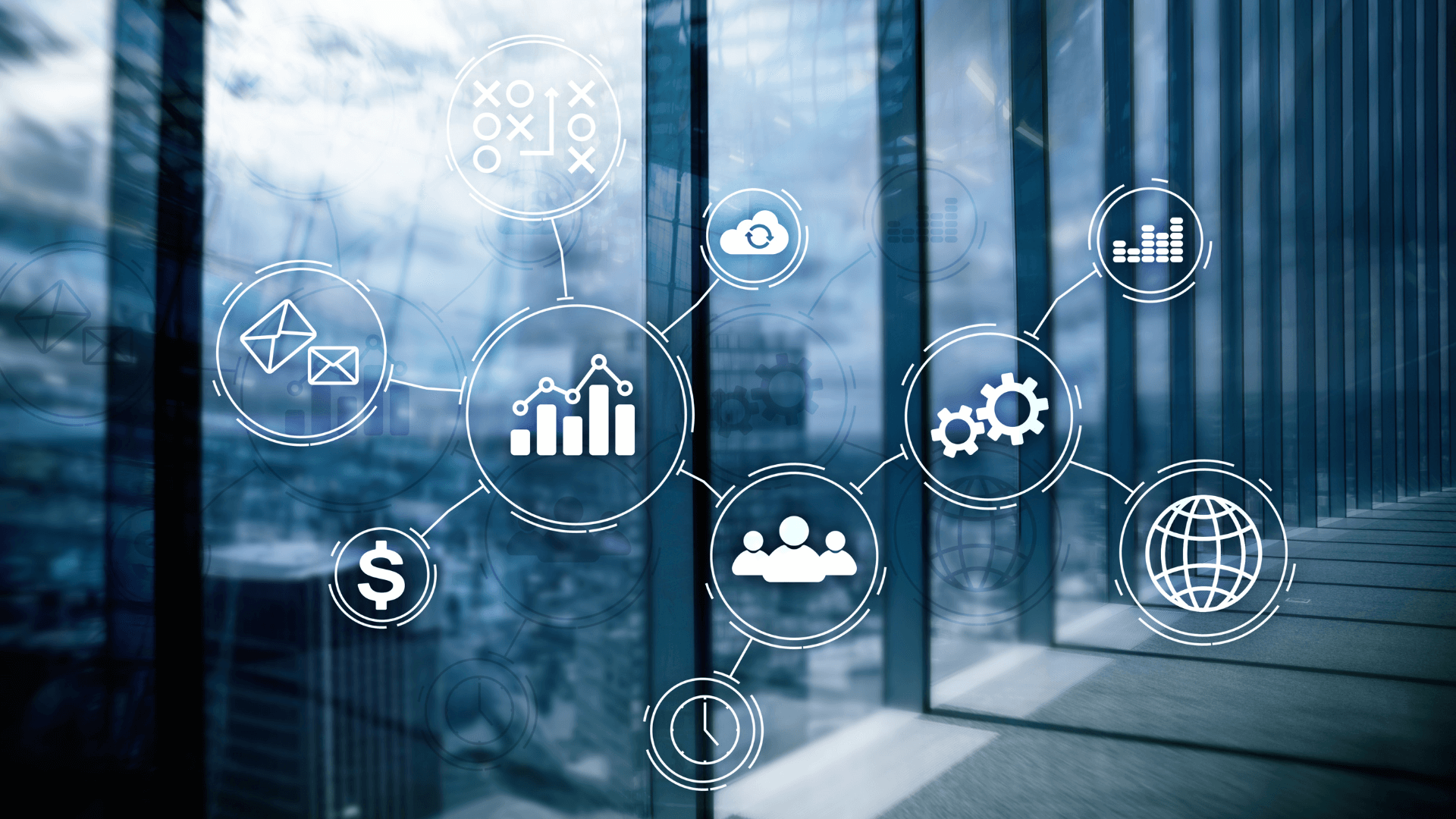
Advanced automation and remote monitoring packages
Advanced automation and remote assistance packages are available for all Diefenbach equipment lines.
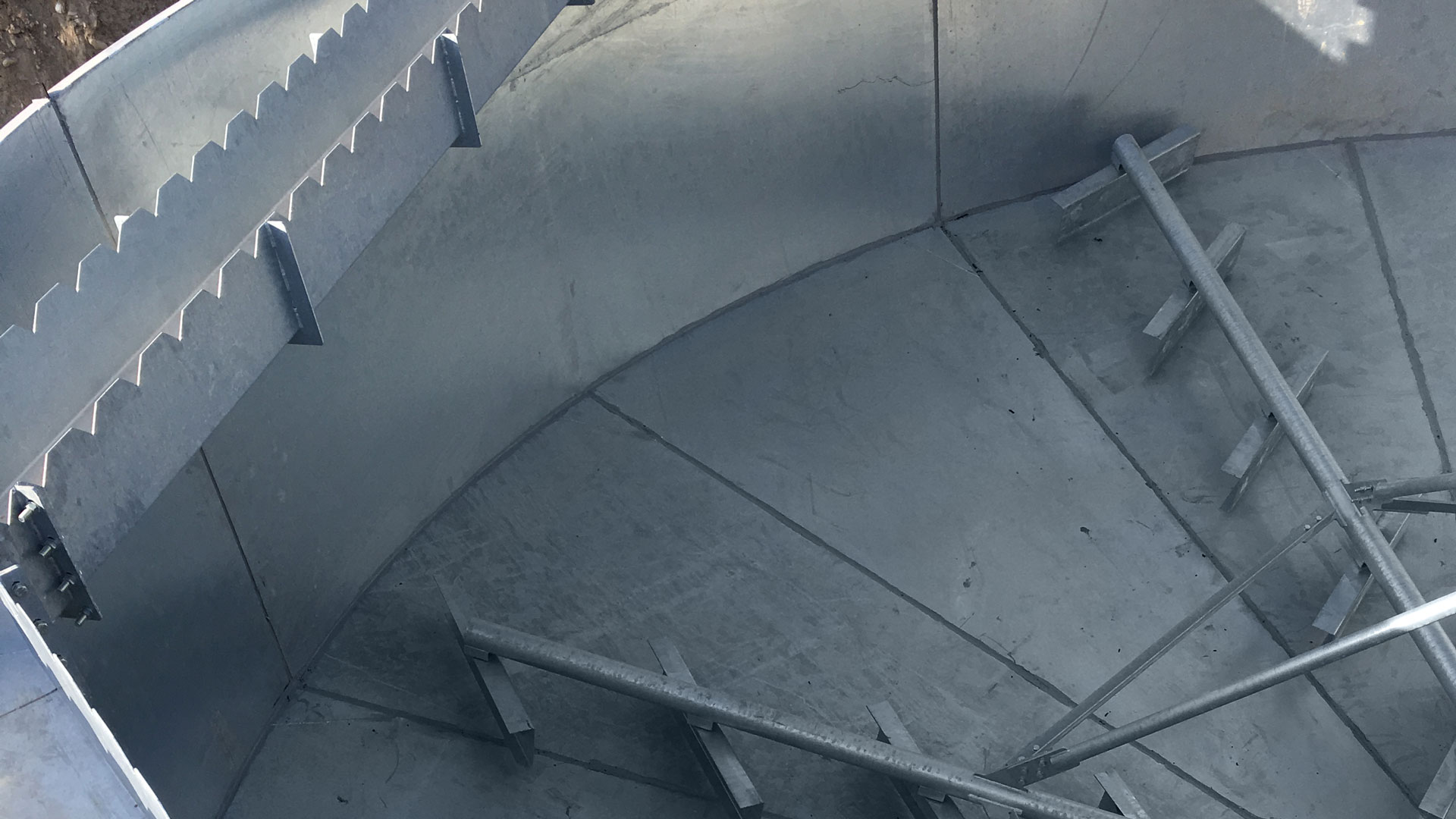
Density monitoring and automated rake lifts
Diefenbach thickeners come with density monitoring systems that allow for optimal control of bed level, underflow density and automation of underflow pumping and rake lift settings.
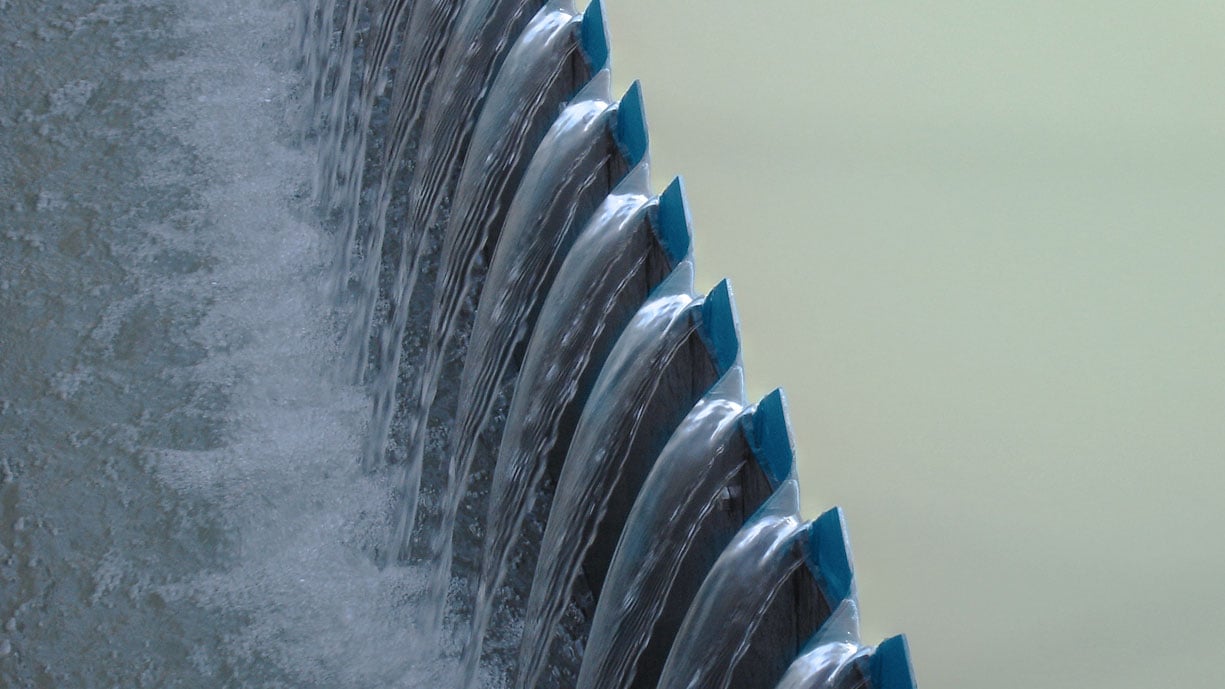
Liquid recovery rates of 85% or greater
Diefenbach thickeners generate a virtually solids-free liquid overflow, which can then be sent for further processing or reused as process liquid elsewhere in the plant, depending on the application.
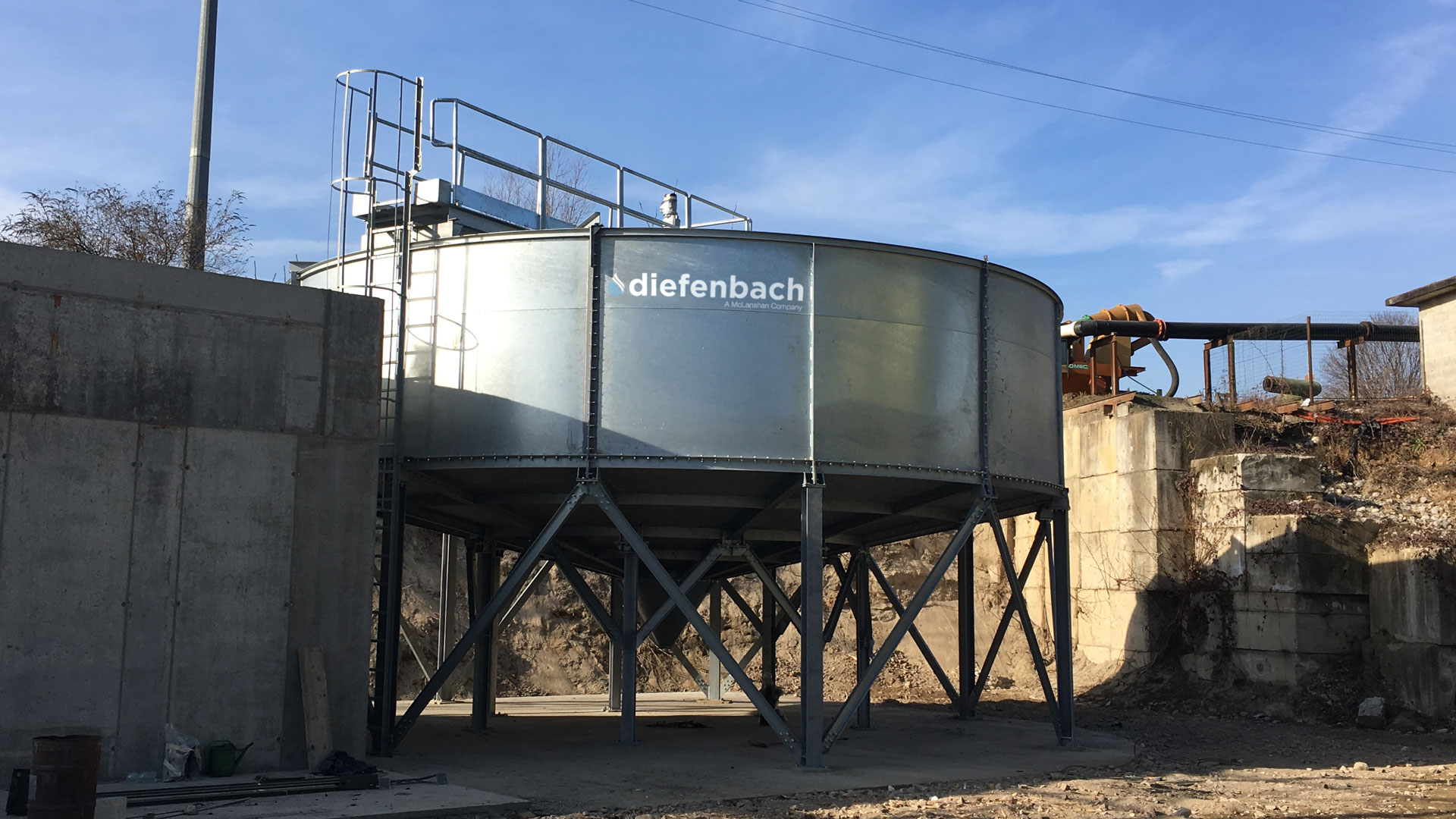
Reduce volume of waste material
Diefenbach thickeners separate the liquid from the solids, generating a denser solids underflow. By separating out the liquid, Diefenbach thickeners can reduce the volume of material reporting to storage or reduce the load on downstream equipment such as a filter press.
Types of Thickeners
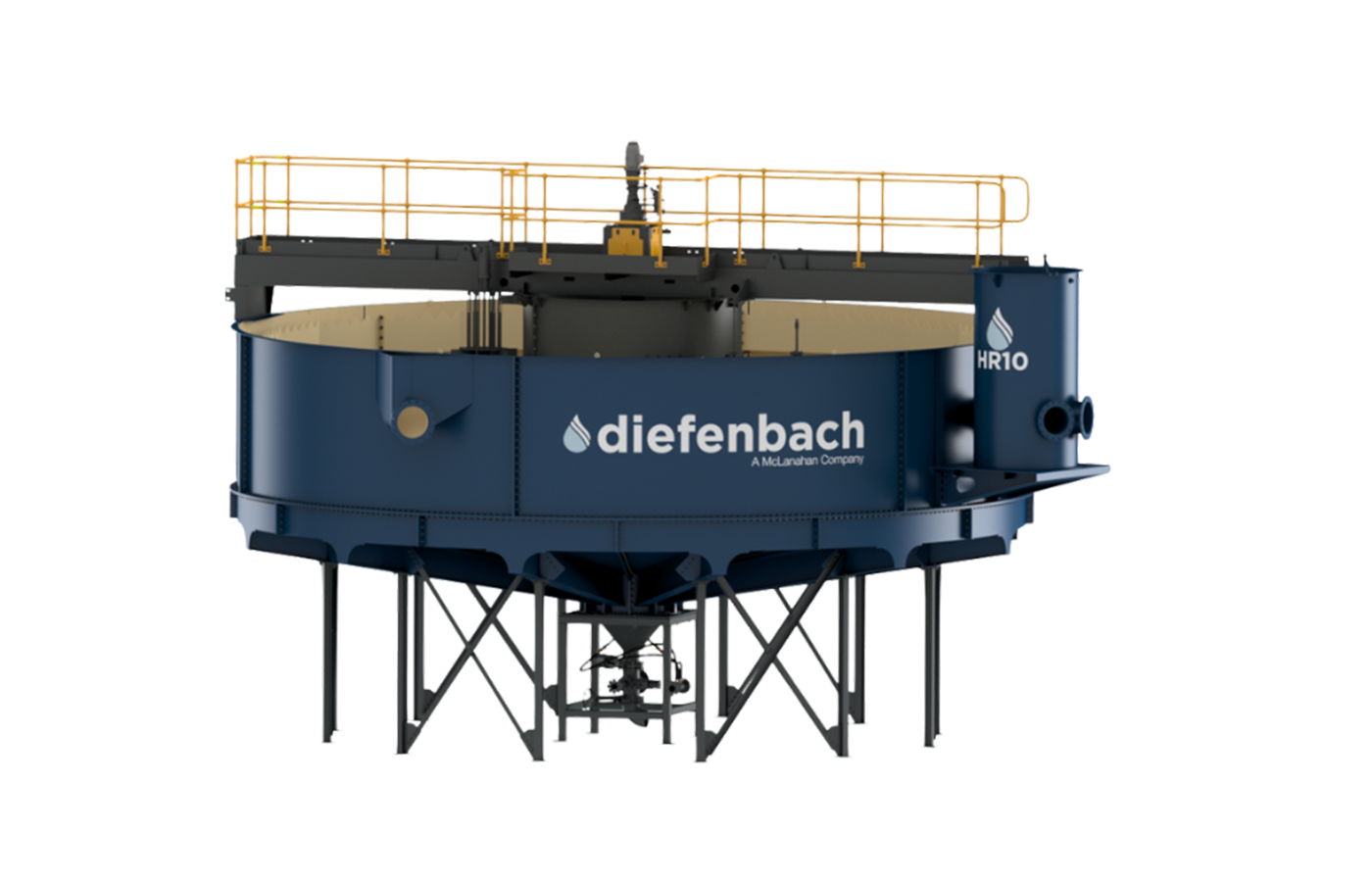
Elevated High-Rate Thickeners - HR Series
Diefenbach HR Series Elevated High-Rate Thickeners are a type of industrial liquid-solid separation equipment used for recovering immediately reusable process water or separating waste solids from leach liquor. This type of thickener features a fabricated sag steel floor on larger diameter tanks and provides open access under the tank for more efficient pumping of the underflow.
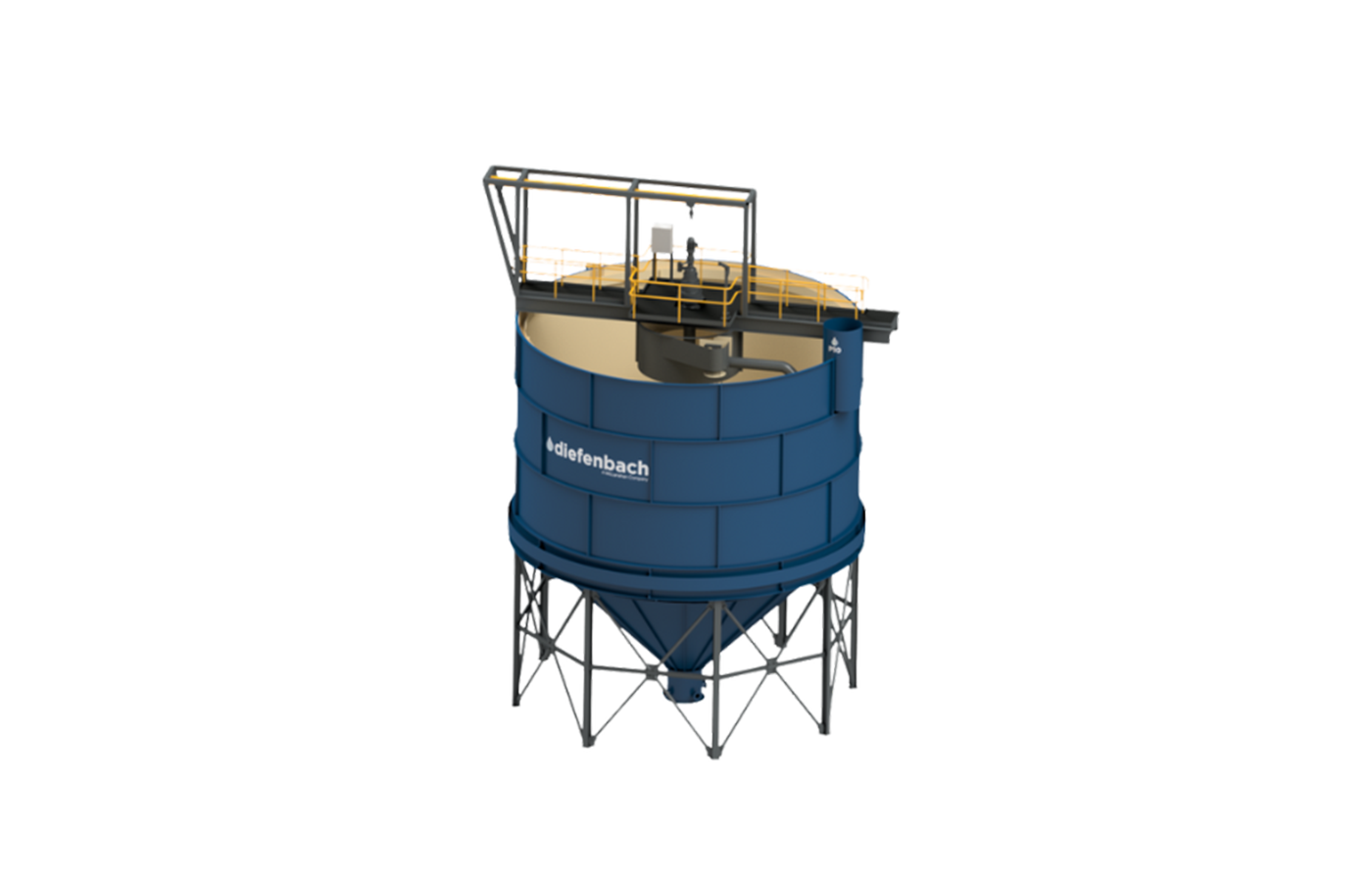
Paste Thickeners - P Series
Diefenbach P Series Paste thickeners are a type of industrial liquid-solid separation equipment that can achieve the highest concentration of solids and maximum recovery of process water or leach liquor.