Filter Presses
Filter presses are a type of industrial equipment used to separate solids from liquids in a slurry. They are used to process a wide range of materials for a variety of industries but are mainly used for clarification, dewatering and filtration in liquid-solid applications.
How Diefenbach Filter Presses Work
Diefenbach Filter Presses consist of two fixed heads – including a feeding side and a drive side, an overhead beam or two side beams, and a moving head containing a pack of vertical rectangular or squared plates with recesses on each side. The fixed head serves as an end to which the feed and filtrate pipes are connected. The moving head moves along the beam and presses the plates together during the filtration cycle by a hydraulic or mechanical mechanism.
Each filter plate is covered with a filter cloth on both sides. When the plates are pressed together, the recessed areas form a series of chambers – the number of which depends on the number of plates in the press. The plates feature a centrally located feed port and two to four filtrate ports running along the length of the entire filter press so that all the chambers of the plate pack are connected together.
The slurry is fed to both ends of the filter press using a pump. As the chambers between the plates fill with the slurry, the solids in the slurry are trapped on the filter cloths, allowing the free flow of the liquid through the cloth to be discharged via the filtrate ports in the corners of the plates. The liquid is then directed toward storage tanks through outlet flanges located in the fixed head of the filter press.
At the end of the filtration stage, the mechanism opens the cylinder slightly to allow dripping. The mechanism then opens the cylinder completely to release the dewatered solid cakes.
Diefenbach offers a variety of plate opening systems that are chosen based on the application. These include manual opening, standard opening, fast opening, instantaneous opening and instantaneous pack opening.
Why Diefenbach Filter Presses
As the leading filtration authority, Diefenbach carefully reviews the details of each application and designs the best Filter Press for handling that application’s feed sludge. Diefenbach offers Filter Presses designed to withstand even the most corrosive of materials as well as Filter Presses that meet ATEX standards for safe use in explosive environments. The company also offers recessed and membrane plates in a variety of materials of construction and sizes, as well as options for core blow, cake drying, cake squeezing, cloth washing and more. Several plate transport systems are also available for handling light to heavy-duty sludges.
Diefenbach Filter Presses are engineered sturdier for greater durability over the years, and they feature one cylinder to close the plate pack, so synchronization is guaranteed. The cylinder features perfect load distribution, which prevents structural deformation. Diefenbach Filter Presses are fully automatic and feature remote connectivity for troubleshooting off site.
With more than a century of experience, Diefenbach backs its equipment with maintenance and support for the lifetime of the machine.
Diefenbach Filter Presses produce millions of tons of filter cake and recycle billions of liters of water every year.
Features & Benefits of Diefenbach Filter Presses
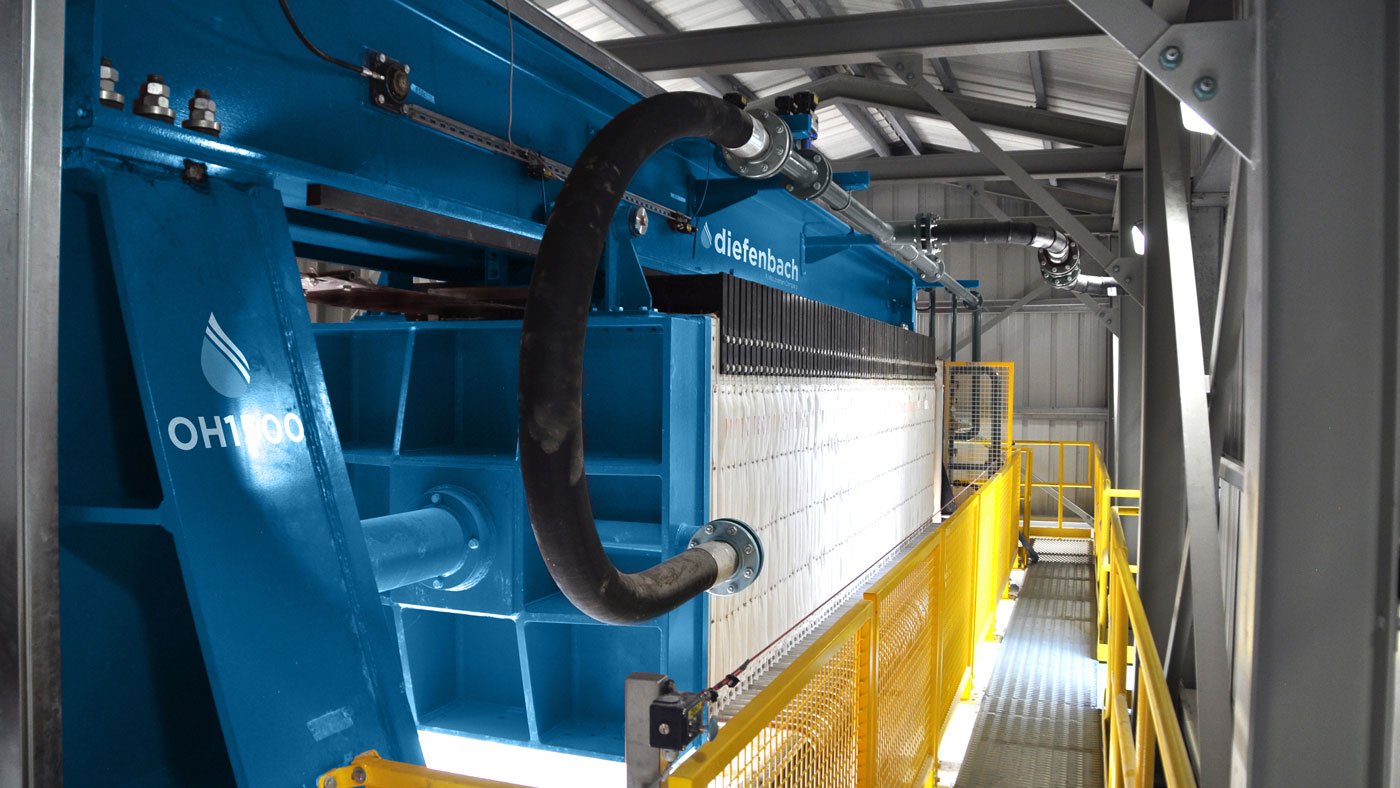
Centuries of design evolution for challenging filtration issues
From mine tailings to sludge from recycling batteries or municipal waste, Diefenbach Filter Presses are engineered to suit the toughest chemical applications and environments.
Diefenbach's experienced engineers are here to solve your toughest filtration problems.
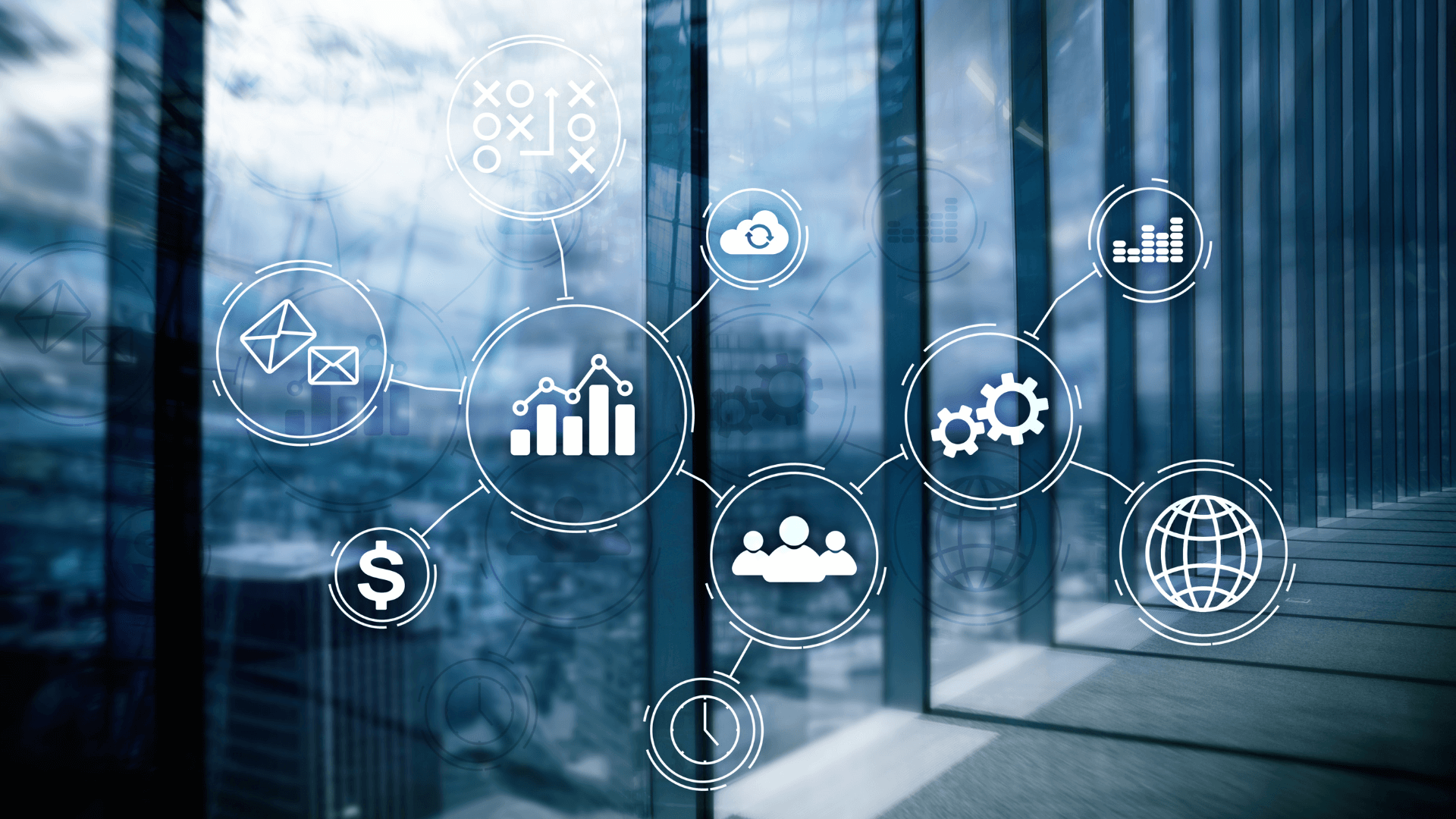
Advanced automation and remote monitoring packages
Advanced automation and remote assistance packages are available for all Diefenbach equipment lines.
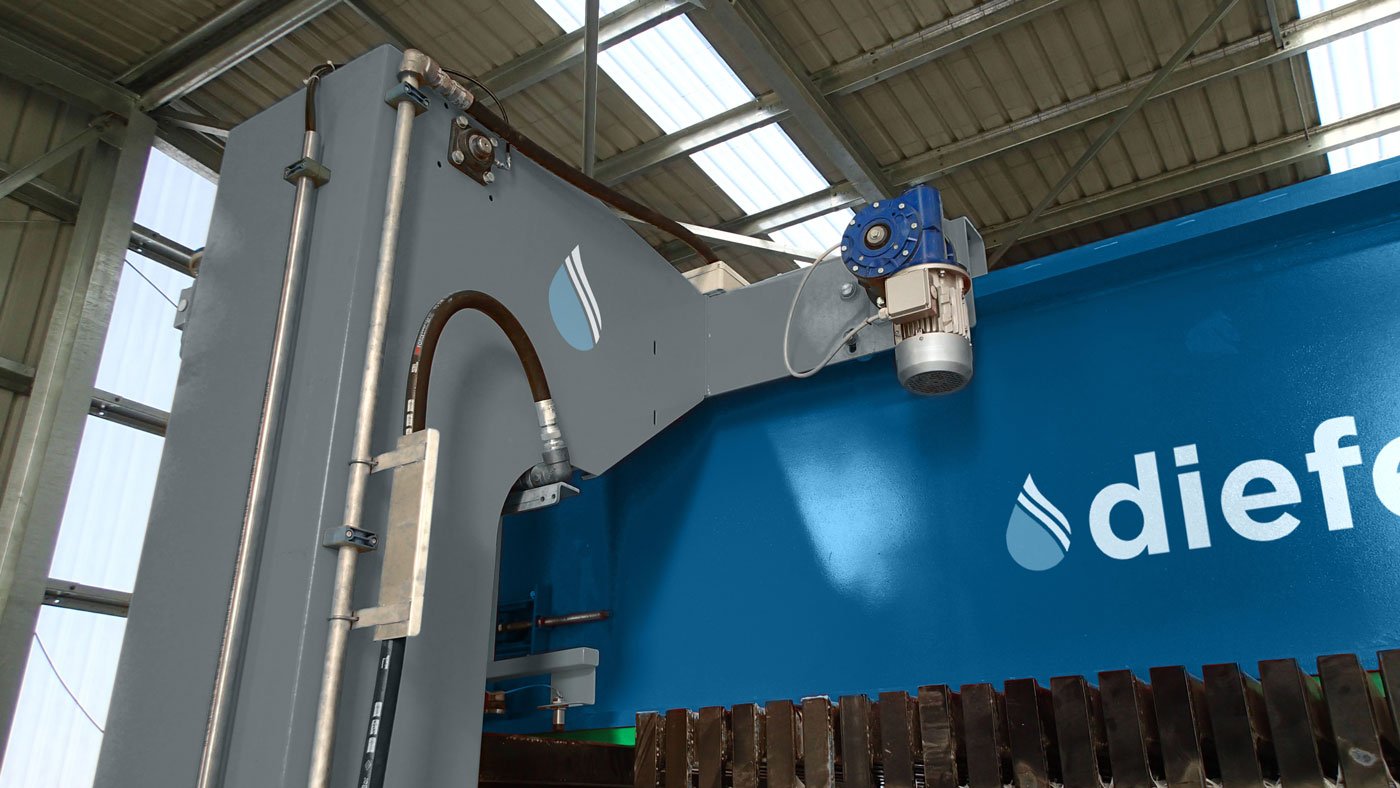
Robotic high-pressure automated wash system
Diefenbach's robotic automatic wash system allows for complete refreshing of the filter cloths at pressures up to 100 Bar (1450 psi).
In highly acid or corrosive environments this reduces the exposure of the plant operators while also increasing life of the filter media.
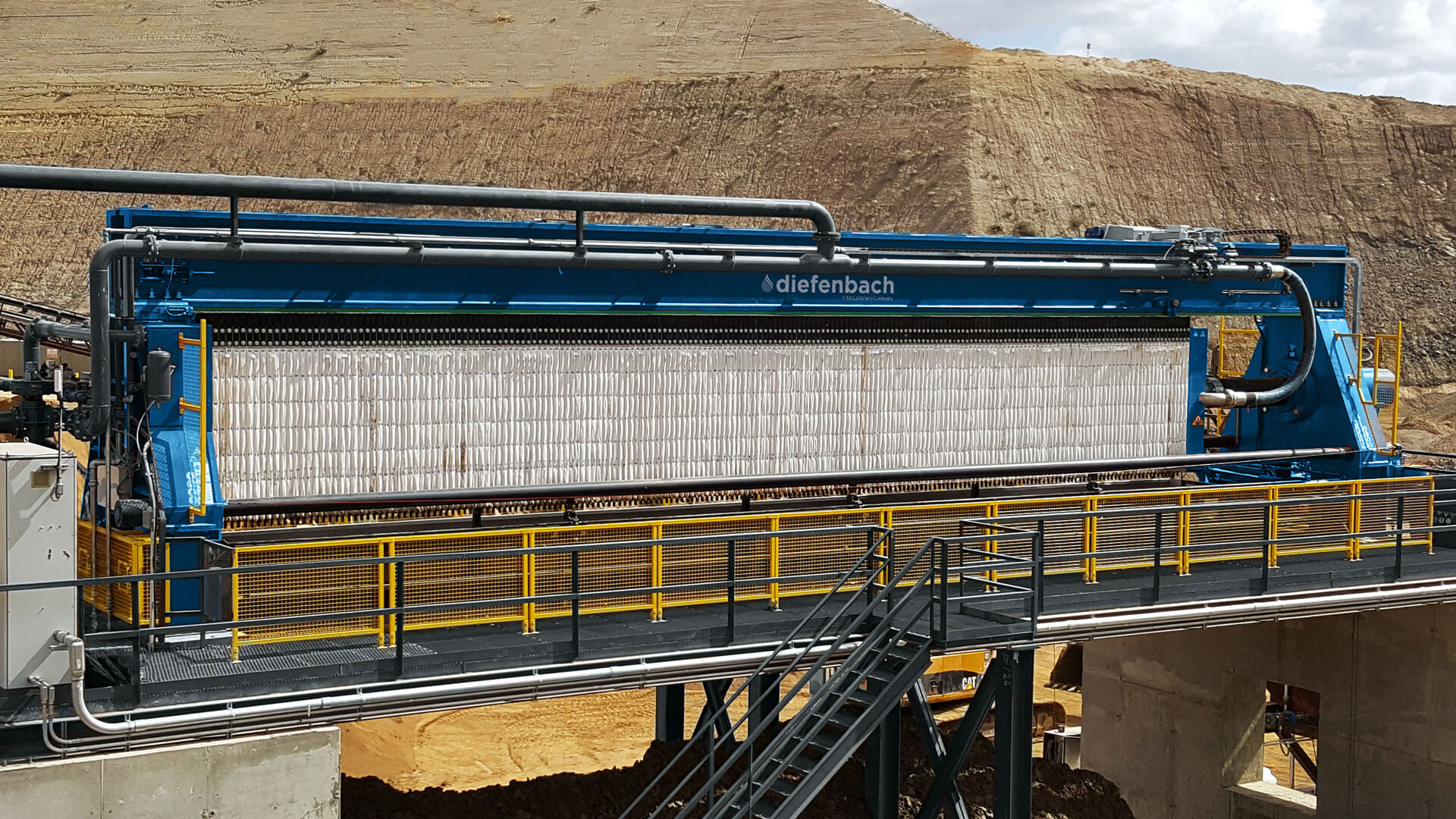
Fully automatic with bidirectional feeding
Diefenbach designs its Filter Presses to be fed from both ends of the press. This improves chamber filling and reduces slurry speed to avoid cloth and plate abrasion. Diefenbach filter presses are fully automatic and do not require an operator.
Additional features
Core blow and cake dry
Diefenbach Filter Presses feature a core blowing step to remove unfiltered slurry residue left in the feed channel prior to the filter press opening. This prevents final product contamination.
Drip tray bomb bay doors
Diefenbach Filter Presses can feature optional bomb bay doors mounted under the filter plate pack to collect the dripping water during filtration and cloth washing and to transfer the water into the filtrate channels.
Plate shaking
Depending on the opening system, Diefenbach Filter Presses feature a plate shaking feature to remove any residue that remains on the filter cloth after the cake has been discharged.
Protection from corrosion
Diefenbach Filter Presses can be treated to protect the components from chemicals and corrosion for handling acidic sludges in applications such as battery recycling.
Types of Filter Presses
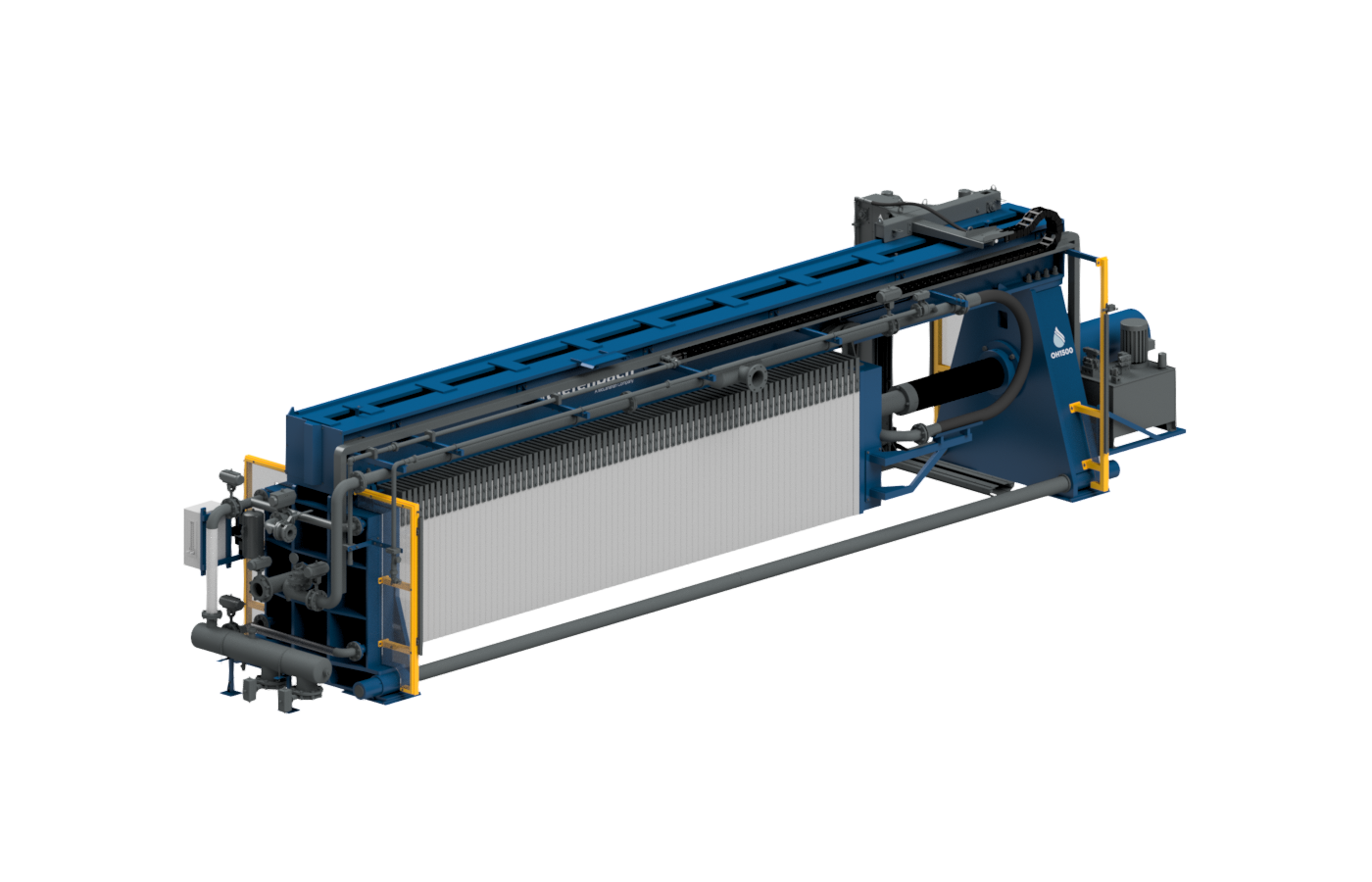
Overhead Beam Filter Presses - OH Series
Diefenbach OH Series Overhead Beam Filter Presses feature an upper beam from which a pack of filter plates are suspended. This type of Filter Press offers greater free space between the plates, allowing for easier access for maintenance and filter cloth changes.

Side Beam Filter Presses - SB Series
Diefenbach SB Series - Side Beam Filter Presses feature two side beams running the length of the press. This style of press is ideal for small to the most challenging applications.
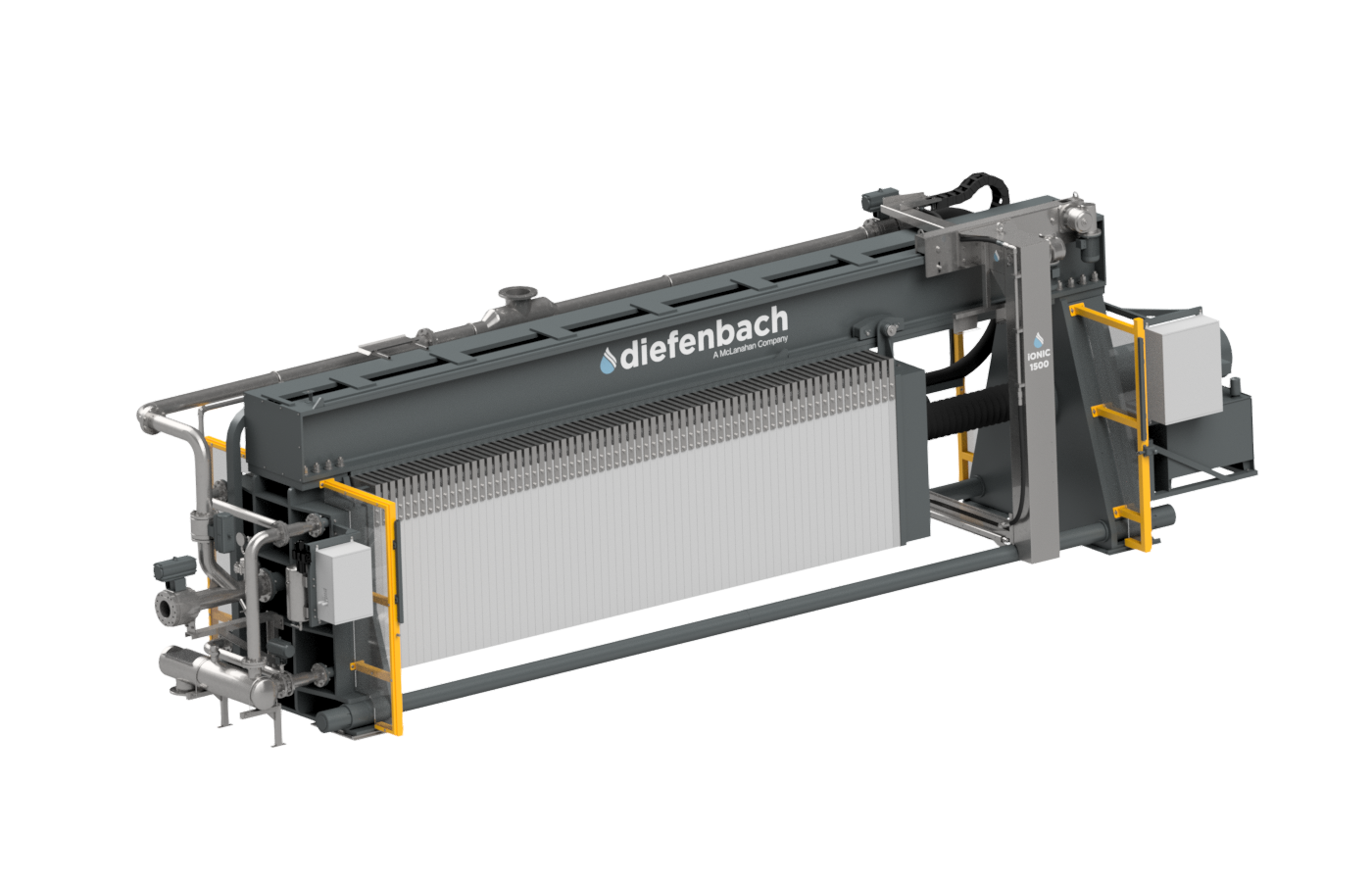
iONIC Series Filter Presses
Diefenbach's iONIC Series Filter Presses are designed to handle sludges that are highly acidic and corrosive. This type of filter press is ideal for use in the lead-acid and lithium-ion battery recycling industry.
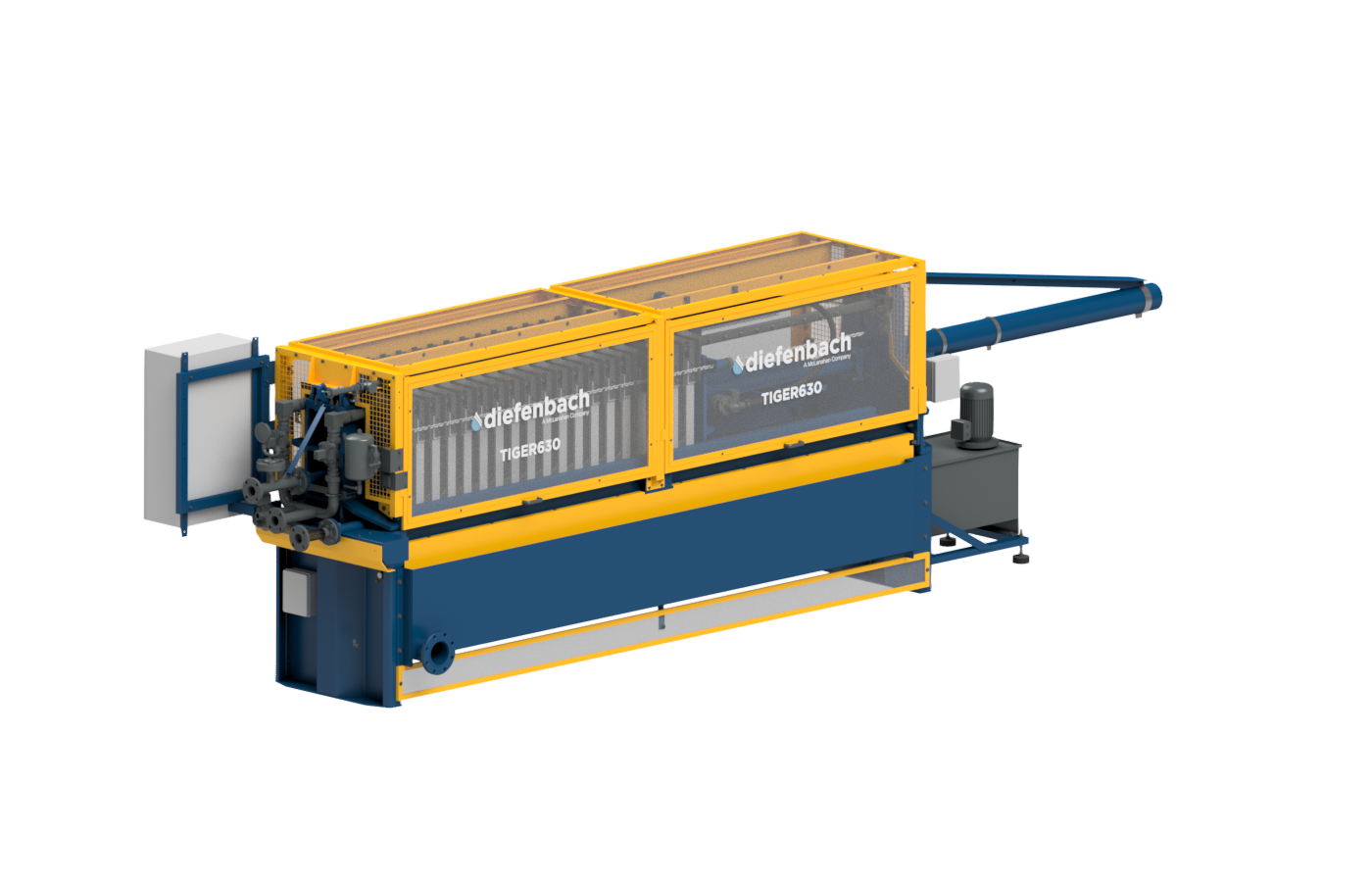
Hybrid Filter Presses - TIGER Series
Diefenbach's TIGER Series of Hybrid Filter Presses offer the benefits of both Overhead Beam and Side Beam Filter Presses. They feature two upper beams running the length of the press.