Battery Recycling
The lead-acid and lithium-ion battery recycling industry is focused on recovering valuable battery minerals for reuse in new batteries.
How Filter Presses Are Used In Battery Recycling
Filter presses are used to separate metals from the sludge or slurry produced during the battery recycling process. The sludge is created from the crushing or grinding of the batteries, which are then mixed with chemicals and water in order to remove the metals. The sludge containing the metals to be recovered is fed into the filter press, which features a pack of recessed plates that when closed together form a series the chambers. As the sludge fills the chambers, the liquid filters through the cloth on the plates while the solids remain inside the press. At the end of a filtration cycle, the plates open and the dewatered solids with the recovered metals are discharged.
Diefenbach engineers filter presses specifically designed for lead-acid and lithium-ion battery recycling. Diefenbach's iONIC filter presses feature a specialized coating to process the press and its components from the highly acidic and corrosive sludges produced during the battery recycling process. These filter presses offer durability and long service life.
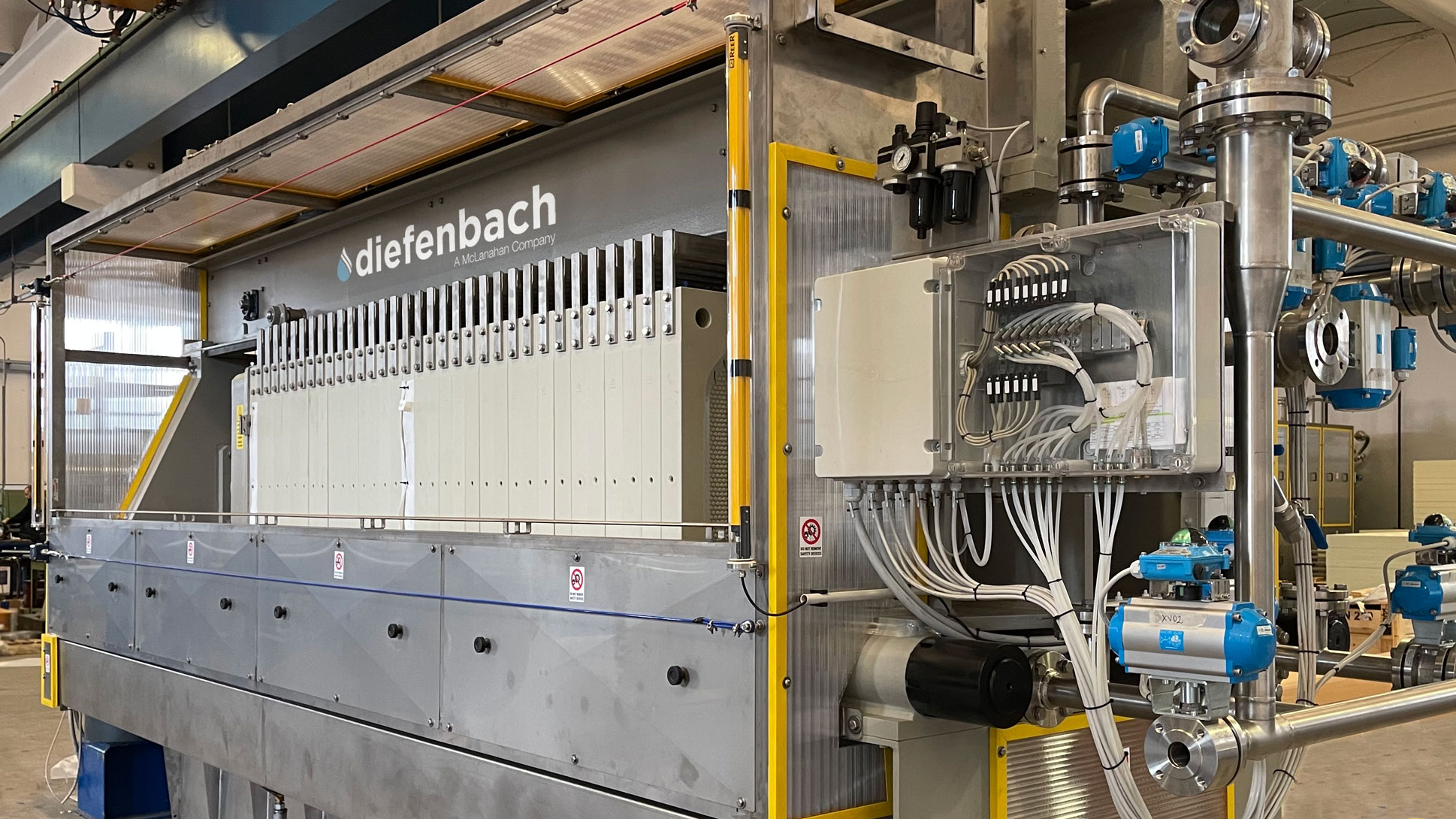
Designed to handle the most acidic and corrosive sludges
Recycling batteries or sludge with highly corrosive or acid slurry? Diefenbach iONIC series filter presses are engineered to suit even the toughest applications.
Depending on the type of batteries being recycled, high-grade stainless steels and specialized coatings are used to protect the filter press from chemical attack.
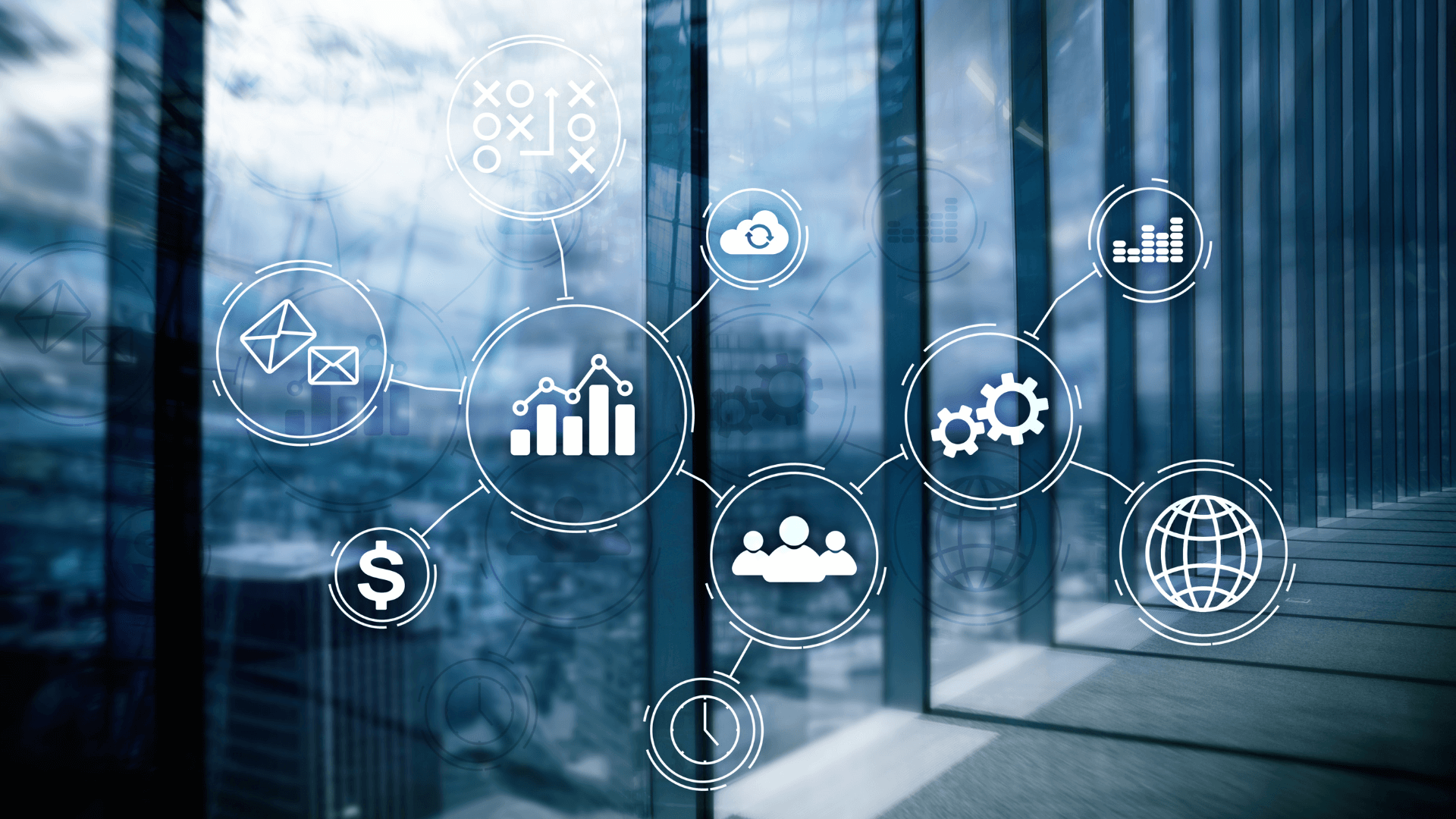
Create a closed-loop system
The liquid separated from the solids in battery recycling applications can be returned to the process, limiting liquid disposal and helping to create a closed-loop system.
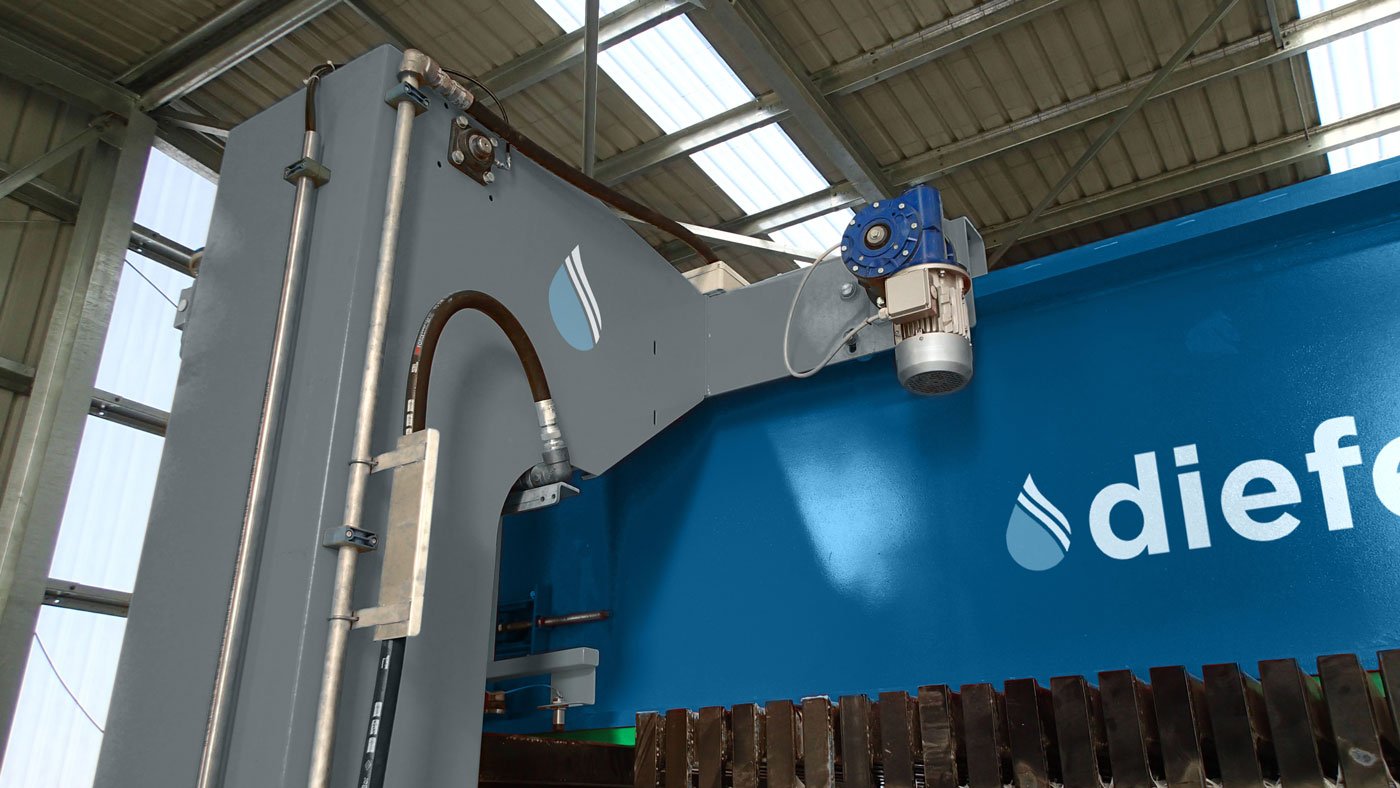
Automatic cloth washing system
Diefenbach's automatic cloth washing system provides a complete refresh of the filter cloths, reducing operator exposure to the sludge and increasing the life of the filter media.