Aggregates
Aggregates are the sand, gravel and rock that have been extracted from the earth and processed for a variety of uses in construction and infrastructure projects, including bridges, buildings, roadways and more.
The processing of aggregate material often involves rinsing, washing and/or scrubbing to remove contaminants from the sound rock. These contaminants can consist of clay, crusher dust, coatings, dirt and other deleterious materials that can cause structural and cosmetic issues in the final aggregate product. These deleterious materials must be removed from the aggregate so that it can meet the required specifications for end use.
The aggregate washing process generates a waste stream that is comprised of the wash water and liberated deleterious material. The waste stream is typically sent to a settling pond, where the solids settle out over time. However, settling ponds can be costly to maintain and take up valuable land space.
Instead of storing the aggregate tailings in a settling pond, mechanical liquid-solid separation equipment is another option for managing aggregate waste. This equipment includes thickeners and filter presses.
How Thickeners Are Used In The Aggregate Industry
Thickeners are used in the aggregate industry to recover clear process water and to thicken the solids for less waste reporting to the settling pond. They are ideal for sites where water is in short supply or expensive to buy and/or sites with space restrictions, environmental or permitting issues, or where ponds are covering up mineable reserves.
Thickeners can be used as the last step in the process before the settling pond or they can be used to prepare the feed ahead of a filter press.
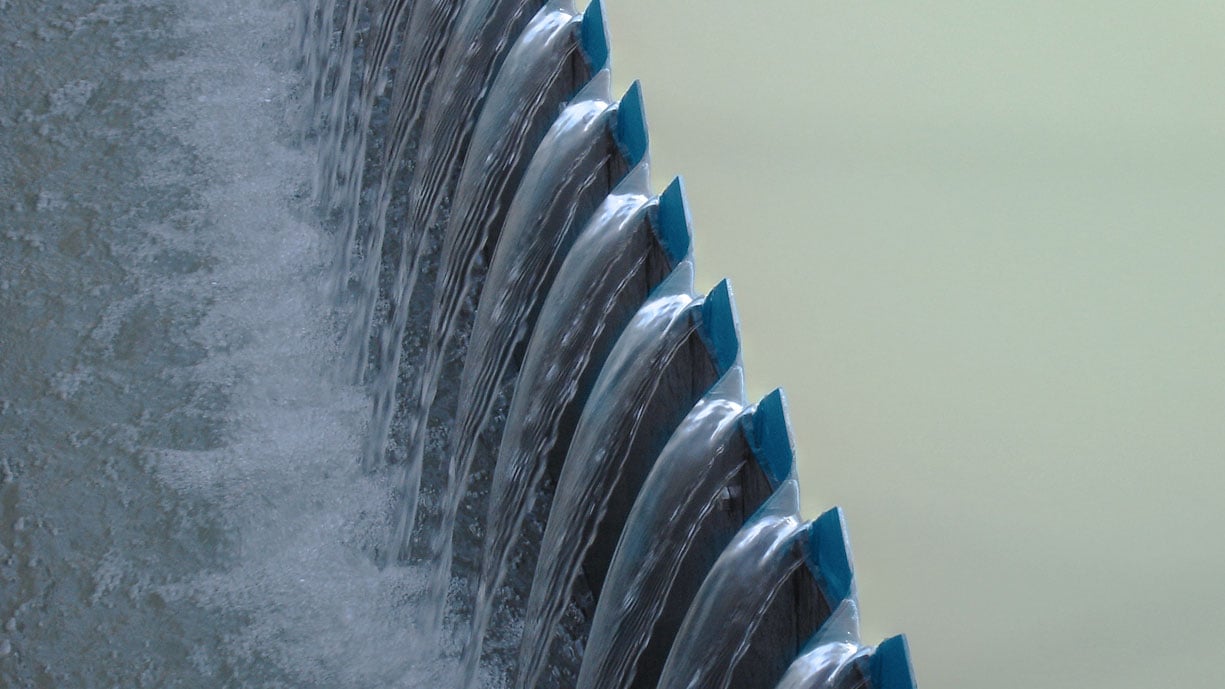
Recover valuable water for reuse
Thickeners can recover the majority of water from the waste stream in sand and gravel applications for reuse in the washing process.
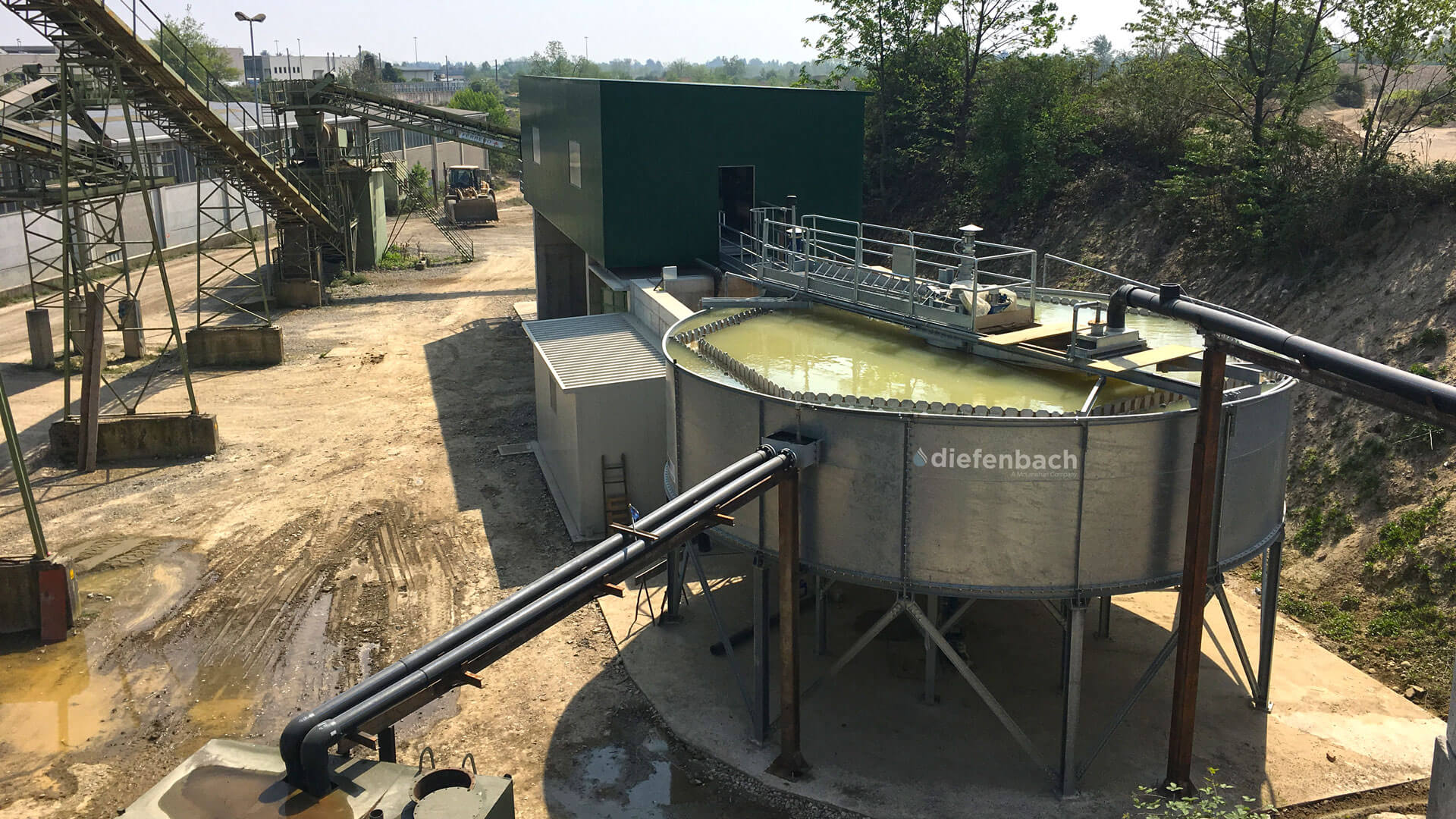
Reduce or eliminate settling ponds
By reducing the volume of material reporting to settling ponds, thickeners are able to greatly reduce the footprint of settling ponds, giving more life to the mine site and preventing the burial of virgin aggregate materials.
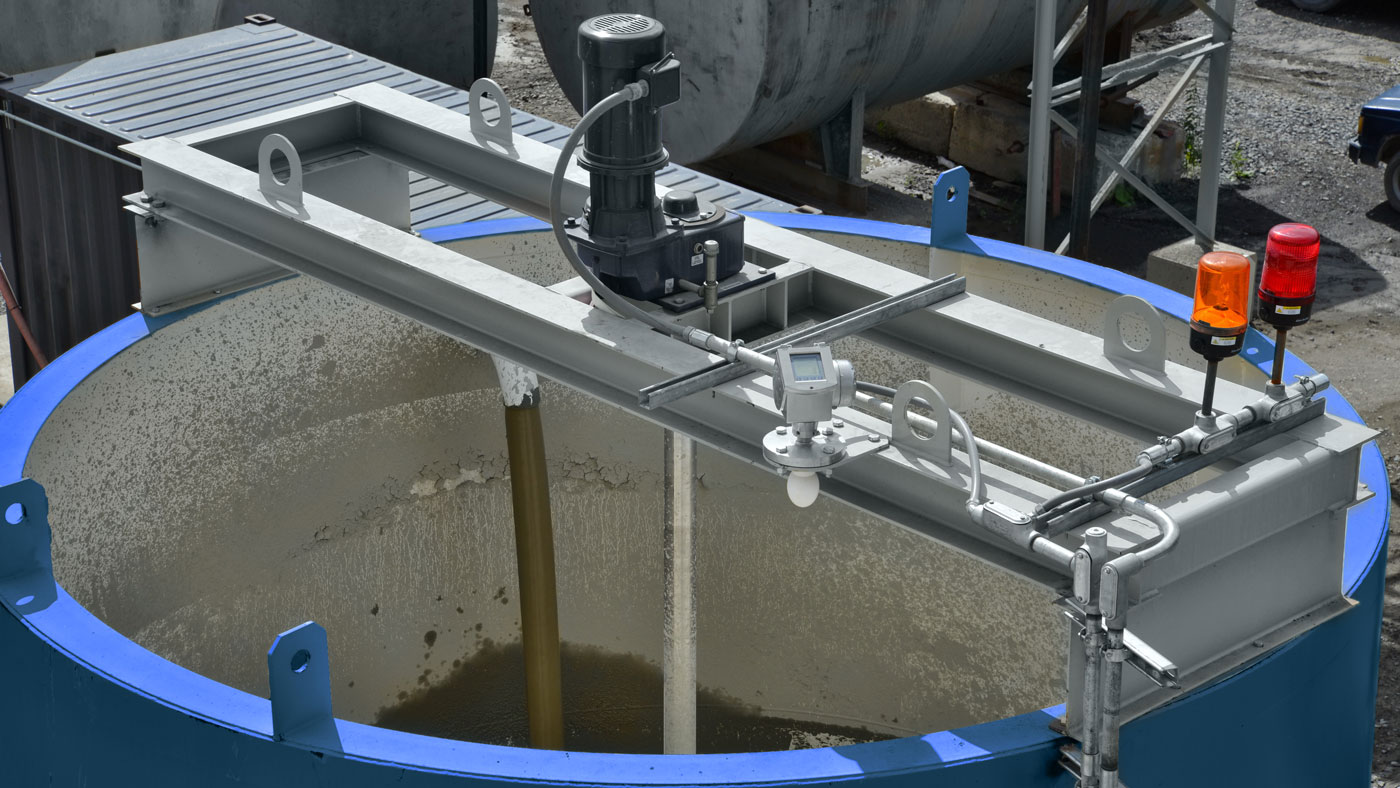
Prepare feed for further dewatering
Thickeners can be used to thicken the solids in the waste stream ahead of downstream processing equipment, such as filter presses, to reduce the size and/or number of equipment required.
Explore Diefenbach's range of thickeners for the aggregate industry
How Filter Presses Are Used In The Aggregate Industry
Filter Presses are used in the aggregate industry to separate the solid particles from the liquid in the waste stream to eliminate settling ponds as well as to simplify tailings management.
Filter Presses generate a drip-free, dewatered solids cake that can be easily managed with mechanical handling equipment. They also produce a solids-free liquid that can be reused immediately as process water in the wash plant.
Because filter presses offer such a high level of dewatering, settling ponds can be completely eliminated when adding this type of tailings management equipment.
Additional benefits of filter presses for the aggregate industry include:
- Freeing up valuable land space
- Helping with environmental/permitting restrictions
- Eliminating settling ponds
- Generating a drip-free, easy-to-handle solids product that is potentially salable
- Recovering immediately reusable process water
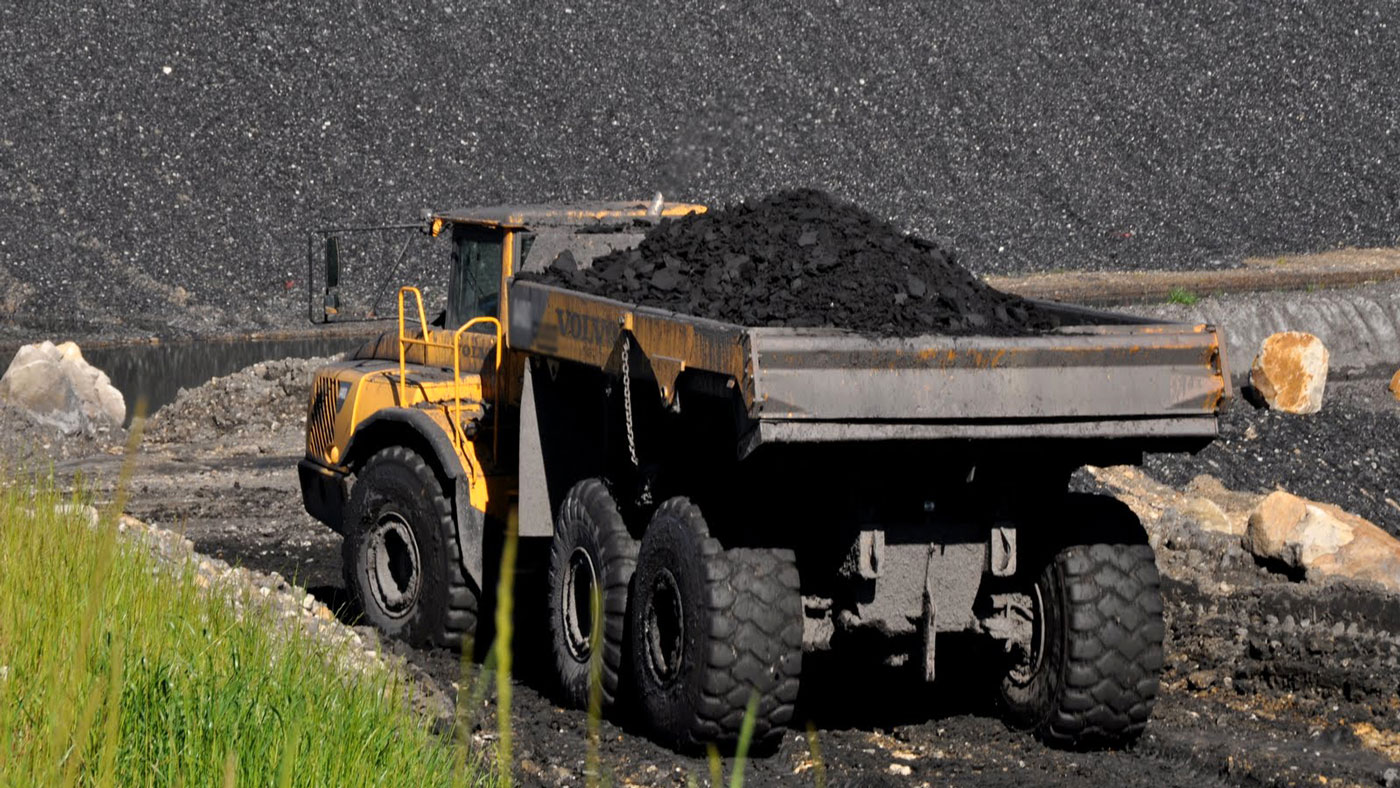
Complete elimination of settling ponds
In aggregate applications, filter presses are able to separate solid particles from the liquid in the waste stream and dewater the solids into ~15-30% moisture cakes. This allows the filter cake to be easily transported for sale as a fill product or capping material or for use in reclamation of the mine site.
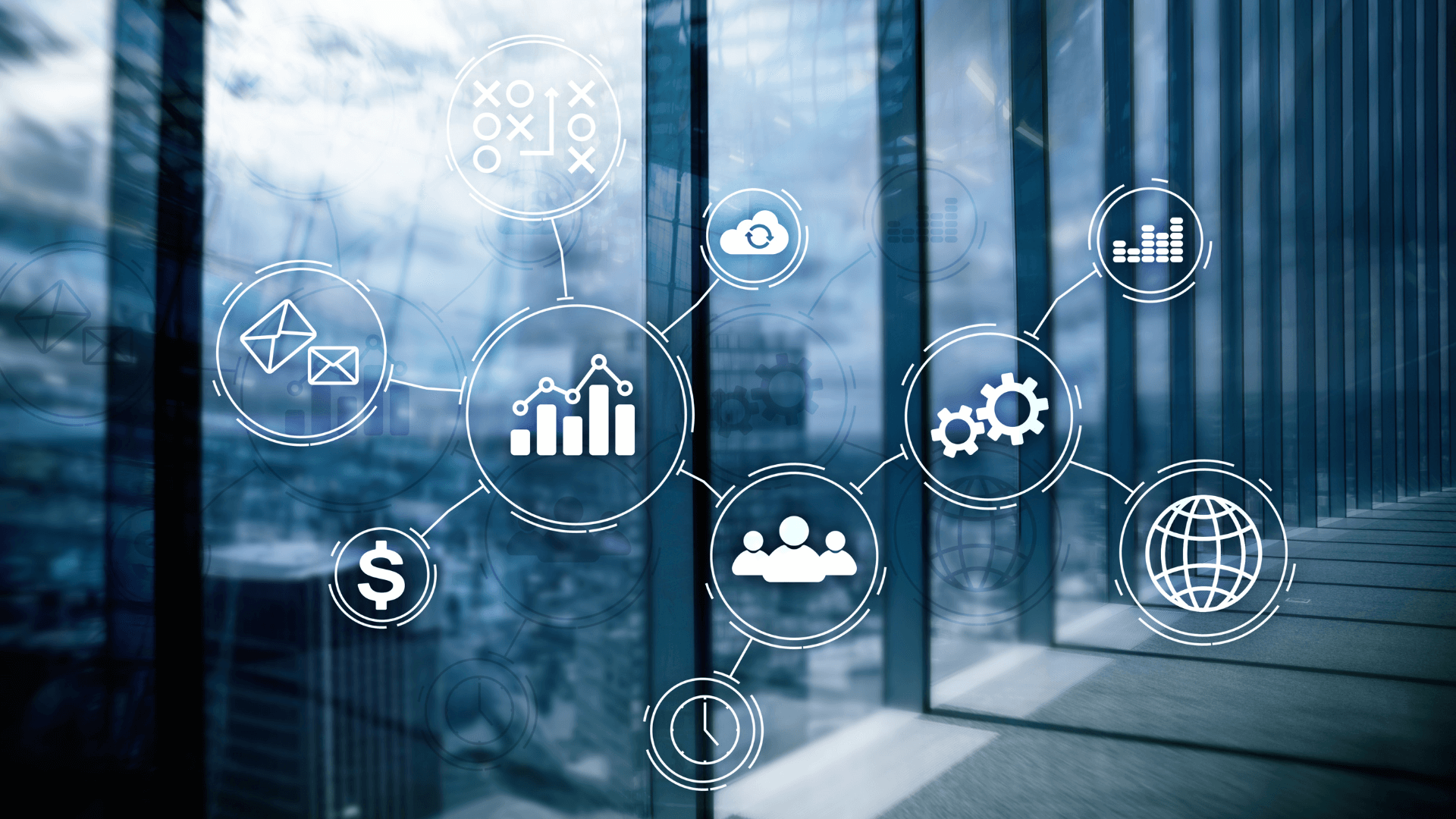
Maximum water recovery
Filter presses provide maximum water recovery for reuse in the washing process. This increases the amount of raw material that can be washed within the limits of the site's water permits.
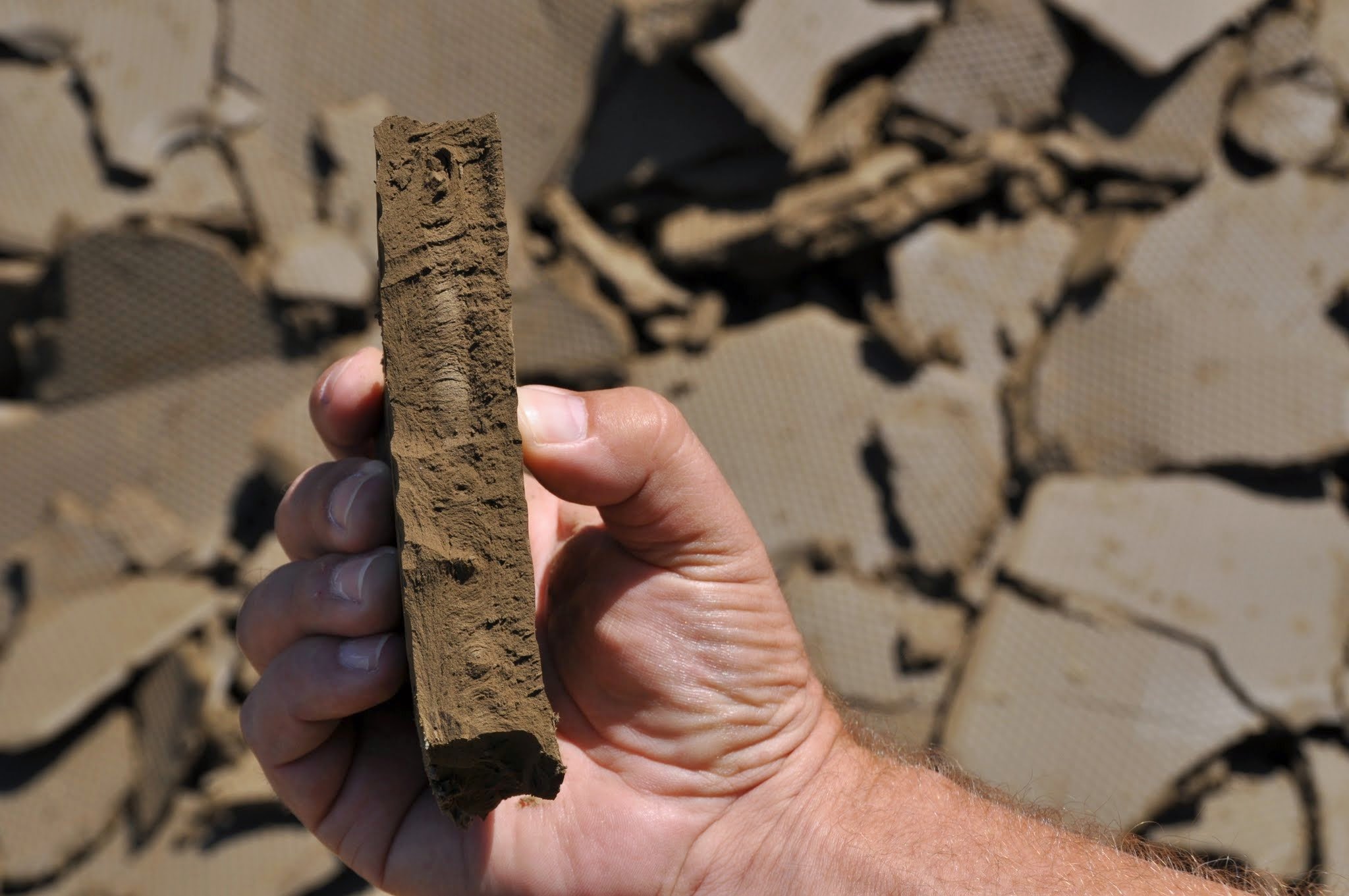
Reduce site permitting timelines and requirements
By using a filter press to eliminate settling ponds, the permitting process is greatly reduced and the amount of water required for to obtain permits is also significantly reduced.