Side Beam Filter Presses
Side beam filter presses are a type of industrial liquid-solid separation equipment used for filtration and dewatering in a wide range of applications. This style of filter press features two beams running the length of the machine located to each side of the filter plates.
How Diefenbach SB Series Side Beam Filter Presses Work
Diefenbach SB Series side beam filter presses feature two side beams running the length of the machine that hold a pack of plates. These plates can be recessed or membrane plates, depending on the application. The plates feature a recessed area on both sides and are covered by a filter cloth.
During a filtration cycle, a moving head attached to the hydraulic cylinder presses the plates together so the recessed areas form chambers with the recessed area on the adjacent plates. The feed slurry is pumped into the filter press and fills the chambers. The liquid in the slurry passes through the filter cloths on the plates and exits the filter press through filtrate pipes.
Meanwhile, the solids are captured on the filter cloth as a filter cake. At the end of the filtration cycle, the plates open to discharge the solids as drip-free cakes. After a plate discharges a cake, it is shaken to remove residue that may remain on the filter cloth.
Once all the cakes are discharged, the plates are pressed together again and another filtration cycle begins.
Why Diefenbach SB Series Side Beam Filter Presses
Diefenbach has been designing and manufacturing filter presses since 1907. The company has an in-house lab, where feed material from filter press enquiries can be analyzed and tested. Pilot filter presses are also available. This allows Diefenbach to select the best filter press for each application, including the type of filter plate and filter cloth, as well as the best process parameters, including filtration cycle time.
Diefenbach filter presses are designed to be sturdy for greater durability. They feature one hydraulic cylinder to prevent structural stresses and to guarantee synchronization of the mobile plate movement. Filter presses manufactured by Diefenbach can also be made to meet ATEX requirements for safe use in hazardous environments, and they can come with several optional features to improve cake dryness and overall maintenance.
With an interface for remote connectivity, Diefenbach filter presses can be monitored off site. They are backed by Diefenbach's commitment to serve its customers for the lifetime of the machine.
Diefenbach began building side beam filter presses in 1907. Since that time, Diefenbach has supplied thousands of side beam filter presses to customers around the world.
Features & Benefits of Diefenbach SB Series Side Beam Filter Presses
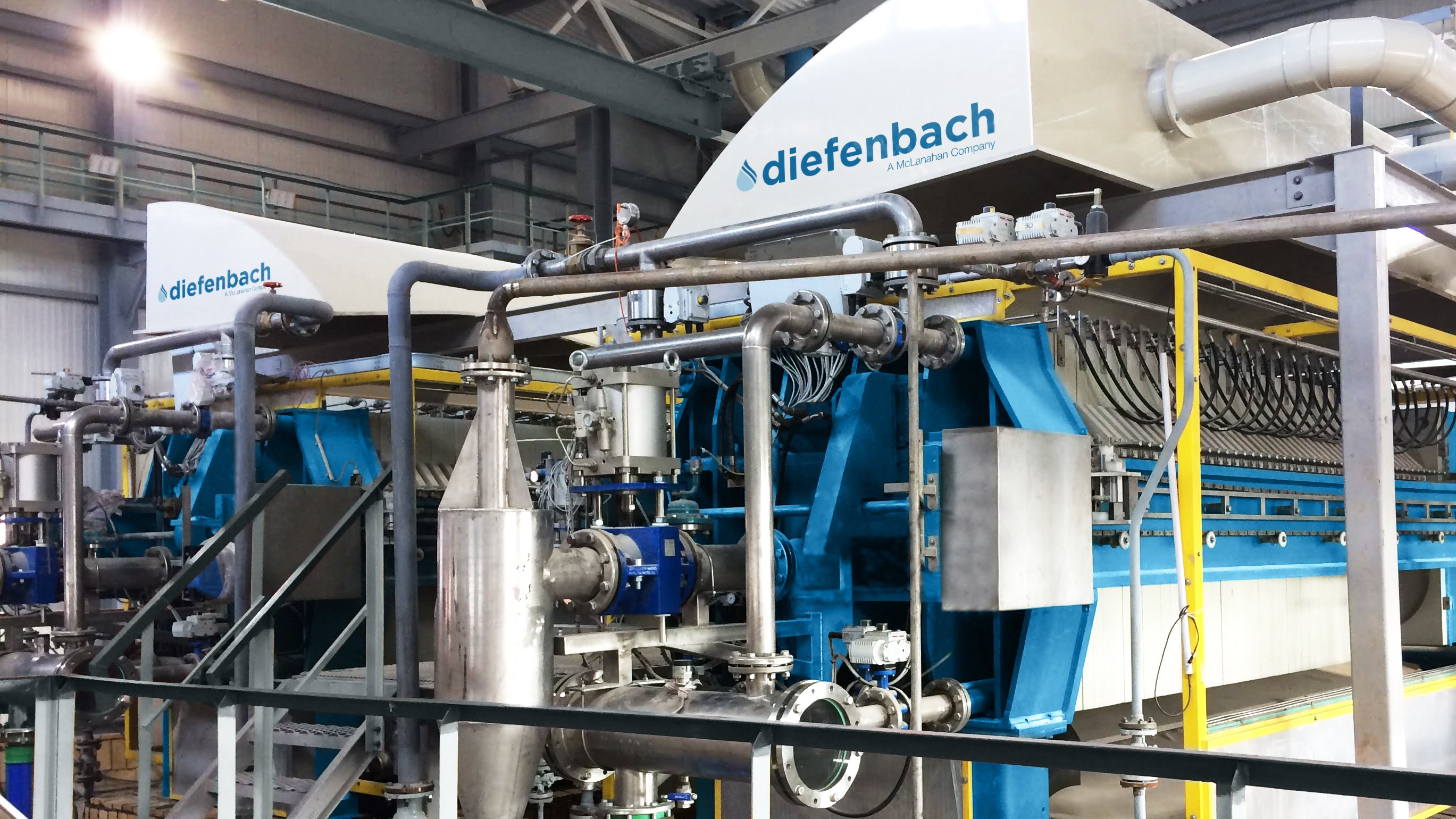
Solving both simple and the most challenging applications for more than a century
Diefenbach side beam presses work well in smaller duty applications that require plates up to 1500mm x 1500mm in size.
Many plate opening styles, cloth washing options and shaking systems are available across the Diefenbach side beam filter press range.
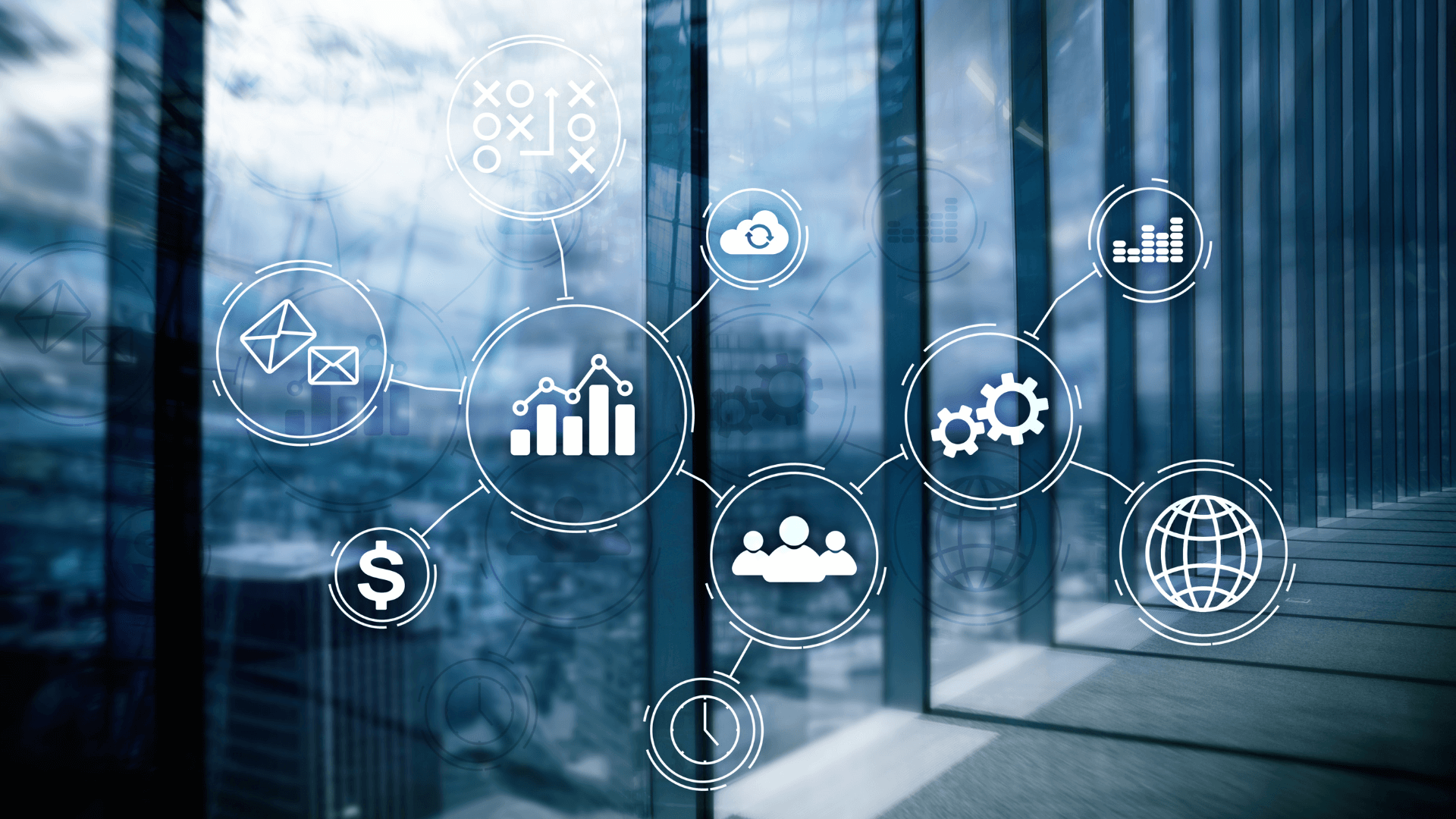
Advanced automation and remote monitoring packages
Advanced automation and remote assistance packages are available for all Diefenbach equipment lines.
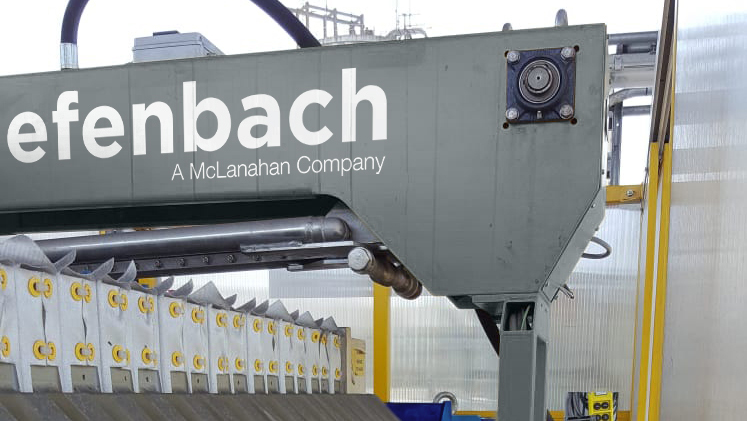
Robotic high-pressure automated wash system
Diefenbach's robotic automatic wash system allows for complete refreshing of the filter cloths at pressures up to 100 Bar (1450 psi). The high-pressure wash option is favored in applications that require deep cleaning once or twice a week.
Diefenbach side beam filter presses feature two choices of automatic cloth washing systems. These systems are designed to remove residue from the filter cloths to extend the life of the filtering cloths and improve operational performance.
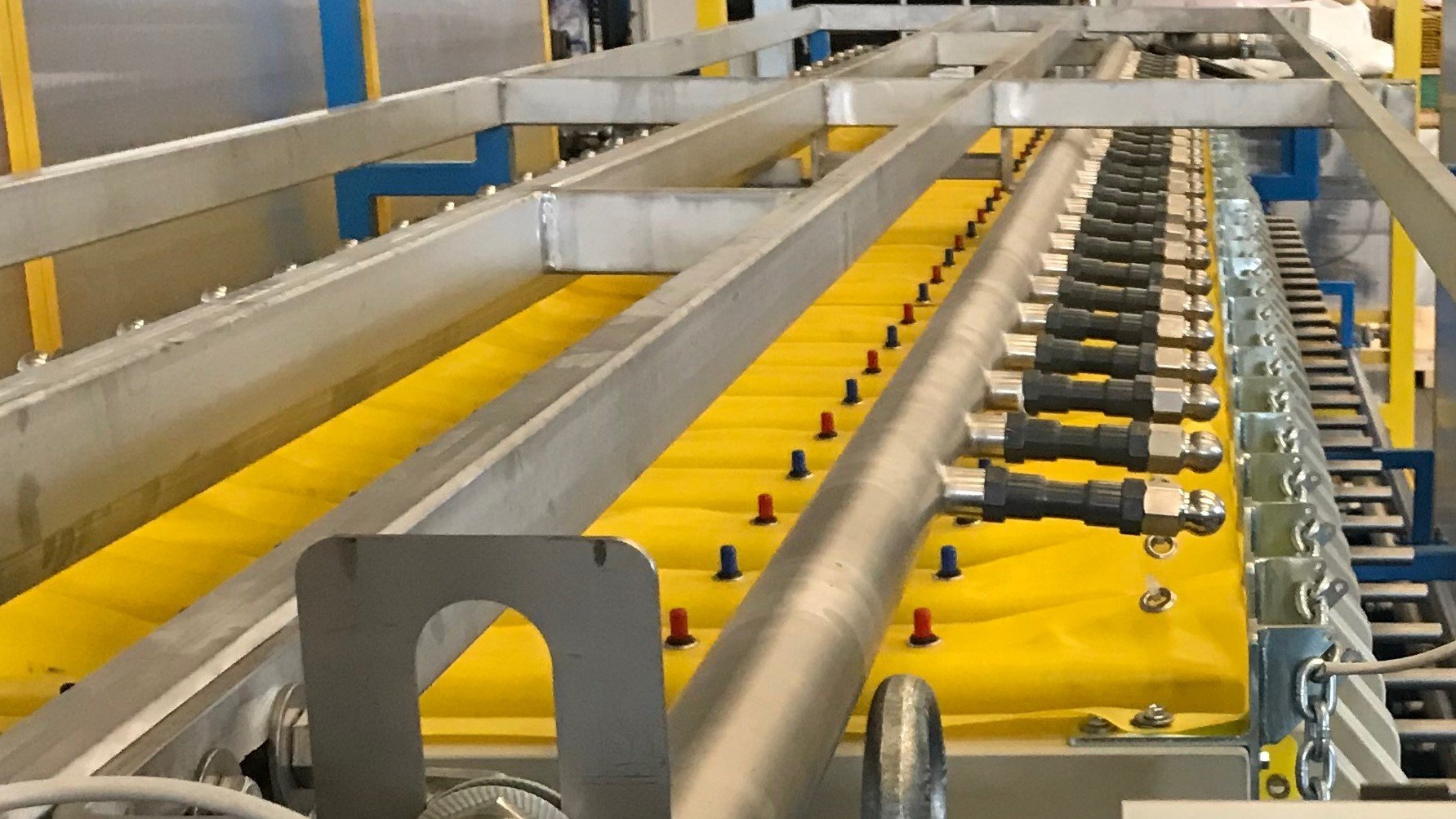
Overhead rapid simultaneous wash system
Diefenbach's overhead rapid simultaneous wash system washes the filter cloths at the end of each cycle. This style wash system is the preferred wash option in applications that require frequent washing such as at the end of each cycle.
Diefenbach side beam filter presses feature two choices of automatic cloth washing systems. These systems are designed to remove residue from the filter cloths to extend the life of the filtering cloths and improve operational performance.
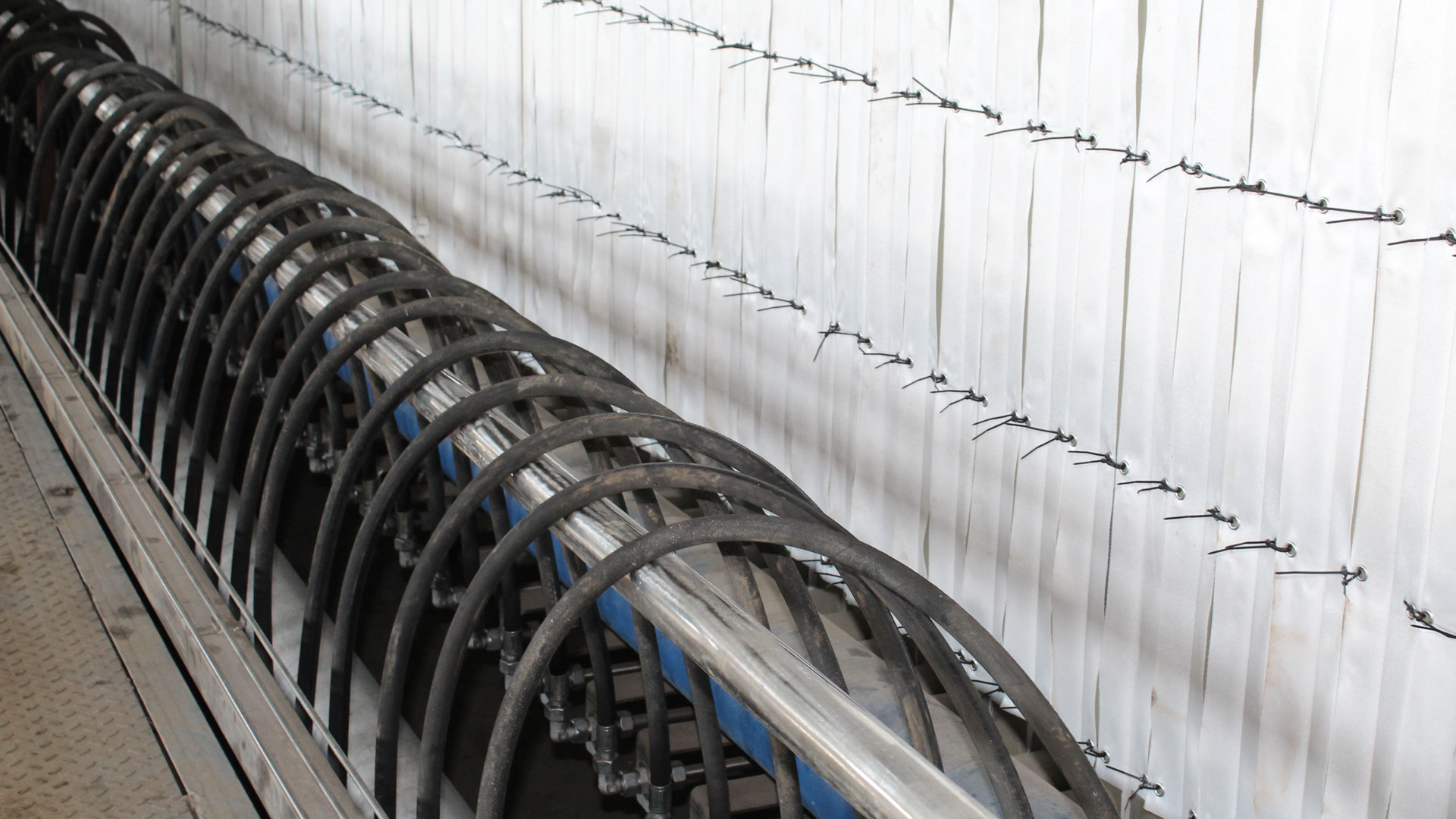
Recessed chamber and membrane plate styles
Diefenbach offers a wide range of cake thickness and plate styles available for complete optimization of the requirements.
Additional features
Dual feed inlets
Diefenbach side beam filter presses are fed from both ends of the press, improving chamber filling and increasing the life of the filter cloths by reducing the inlet velocity (half the velocity vs. single fed entry). This greatly improves filter cake consistency from end-to-end and also significantly increases the life of the filter media.
Core blow system
Diefenbach side beam filter presses feature a core blow system that allows for the removal of the slurry residue in the central filling port prior to cake discharge. This step improves cake dryness as well as reduces build-up of material along the sealing edges of the filter plates.
Explosion-proof versions available
Diefenbach side beam filter presses can be designed to meet ATEX standards for safe use in hazardous and explosive environments.
Plate shaking device
Diefenbach side beam filter presses feature a plate shaking step that helps to remove any cake residue left on the filter cloths after the plates are discharged.
Rapid opening and synchronization guarantee
Diefenbach side beam filter presses feature only one cylinder on the main drive. This reduces structural stresses and guarantees plate synchronization as well as increasing the throughput of the machine through faster opening and closing times.