Overhead Beam Filter Presses
Overhead beam filter presses are a type of industrial filtration equipment used for liquid-solid separation and dewatering. They consist of an overhead beam from which a series of plates are suspended. When the slurry to be separated is pumped into the filter press, the liquid passes through the filter cloths attached to the plates while the solids in the feed are captured on the cloth and discharged as dewatered cakes.
How Diefenbach OH Series Overhead Beam Filter Presses Work
Diefenbach OH range of overhead beam filter presses feature a pair of overhead beams with a sliding system of suspended plates. The plates are recessed on both sides and can optionally include a fixed or removable membrane for further liquid removal. When the plates are held together via the hydraulic or mechanical mechanism, the recesses form a series of chambers.
Slurry material is pumped into the chambers from both sides of the filter press. The liquid in the slurry passes through filter cloths on the plates and into a storage tank, while the solid material is captured on the cloths as a filter cake. If equipped with membrane plates, water is inserted between the internal surface of the plate and the membrane to squeeze the cake and recover additional liquid.
At the end of the filtration stage, a core blowing of the central feed port removes slurry residue to improve cake dryness. An optional cake drying step introduces compressed air into the filter press to improve the dryness of the solid material before discharge.
The plate transport mechanism then opens the cylinder to release the solid cakes. Diefenbach offers several options of plate transport devices for overhead beam style filter presses, including standard plate opening, fast plate opening and instantaneous pack opening. The best opening system depends on the feed sludge and the application.
Why Diefenbach OH Series Overhead Beam Filter Presses
Diefenbach OH range of overhead beam filter presses provide the structural simplicity and robustness required for all types of applications involving liquid-solid separation. These fully automated machines offer easy maintenance and operation. They also can be designed to meet ATEX standards for explosive environments as well as to withstand the processing of acidic and corrosive materials for applications such as battery recycling.
Diefenbach overhead beam filter presses offer easy cloth changing without the need to remove the filter plates. This makes the process for changing out a filter cloth fast and easy.
With more than 100 years spent designing and manufacturing filter presses, Diefenbach has become the leading filtration authority. Each application is carefully reviewed and the feed sludge is tested in Diefenbach’s in-house lab so that Diefenbach can recommend the best filter press for the application.
Diefenbach overhead beam filter presses are available with either recessed chamber or membrane plates in a wide range of sizes for handling small to large capacities. Several plate transport systems are also available for handling light to heavy-duty sludges.
With a robust and time-proven design, Diefenbach's range of OH Series overhead beam filter presses are trusted by customers around the world to recycle billions of liters of water.
Features & Benefits of Diefenbach OH Series Overhead Beam Filter Presses
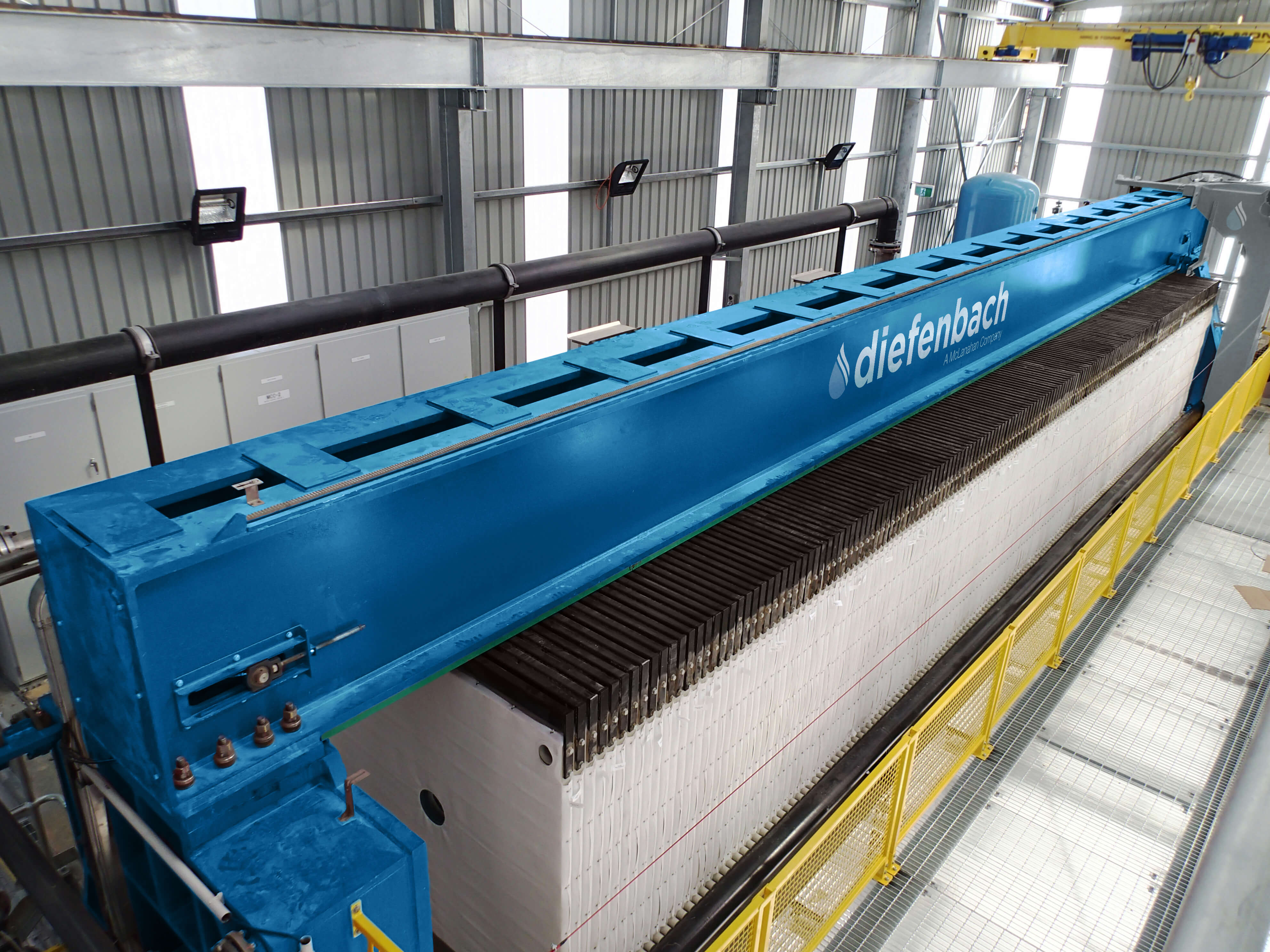
Robust overhead beam design proven over decades in the most demanding applications
Diefenbach's overhead beam filter press design has been in use for decades with a proven history of long-term reliability and ease-of-maintenance.
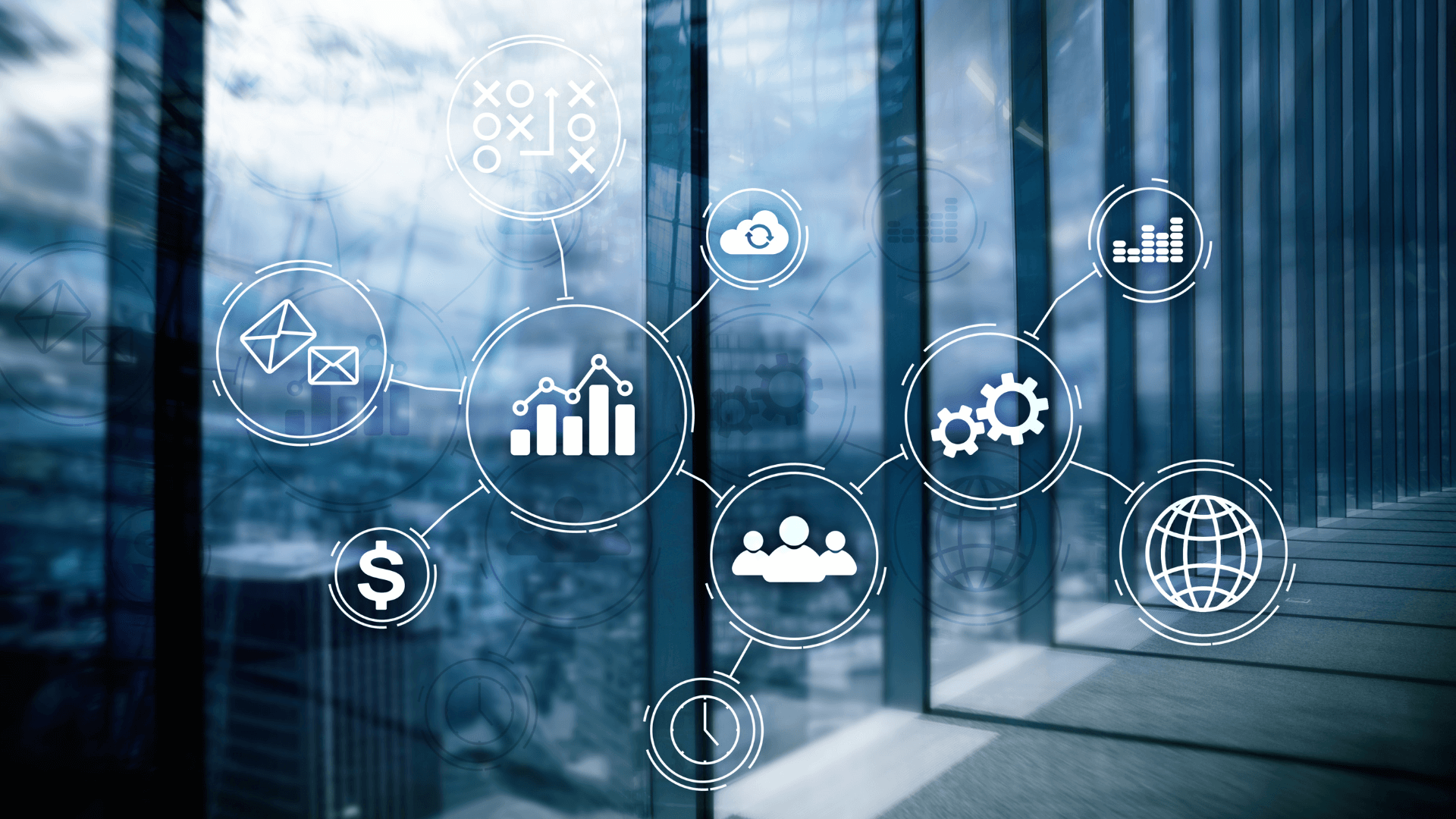
Advanced automation and remote monitoring packages
Advanced automation and remote assistance packages are available for all Diefenbach equipment lines.
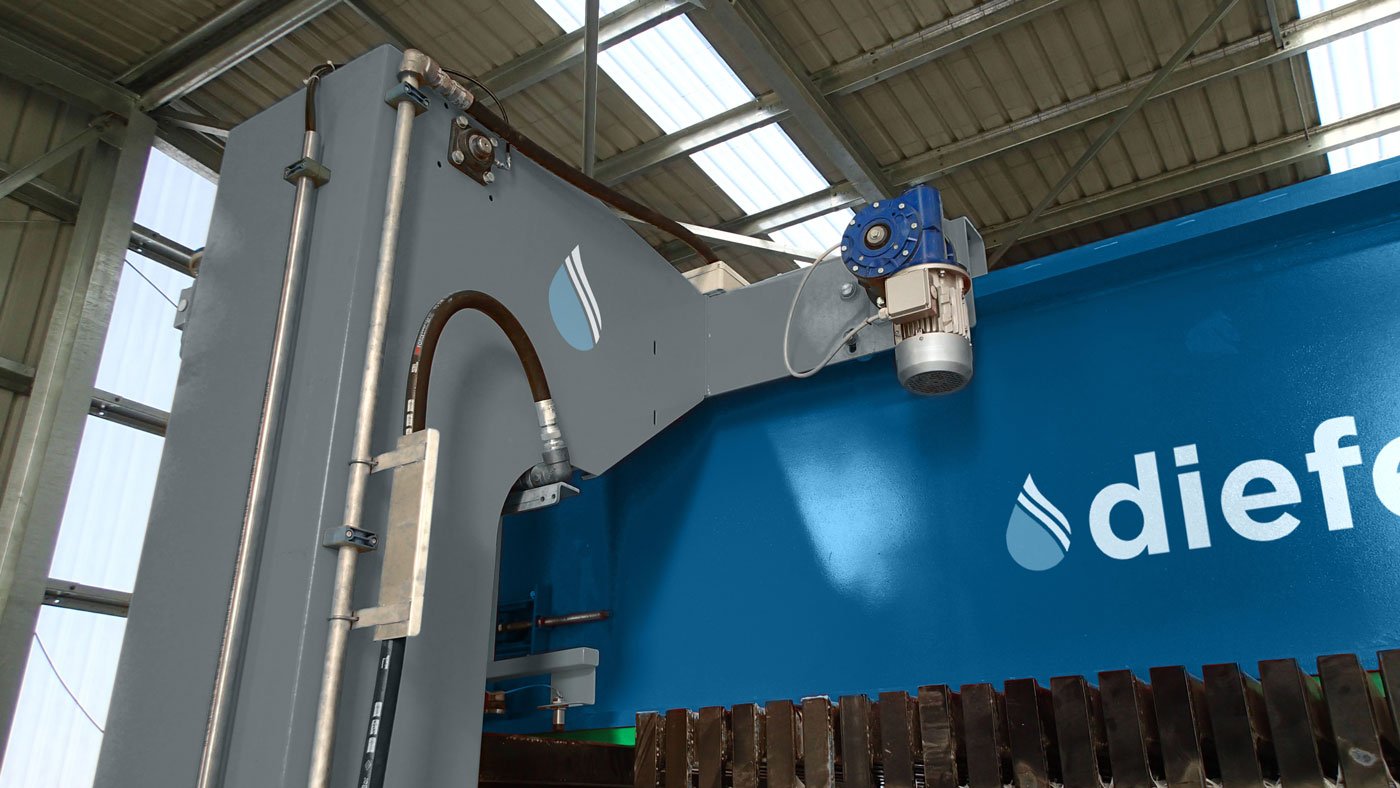
Robotic high-pressure automated wash system
Diefenbach's robotic automatic wash system allows for complete refreshing of the filter cloths at pressures up to 100 Bar (1450 psi).
Automating the wash system frees up operators to focus on production and ensure the life of the filter cloths is maximized. High-pressure wash using robotic spray arms provides a much deeper and thorough wash than what can be achieved manually. This makes it the ideal solution for most applications to ensure maximum filtration performance as well and minimum operating costs.
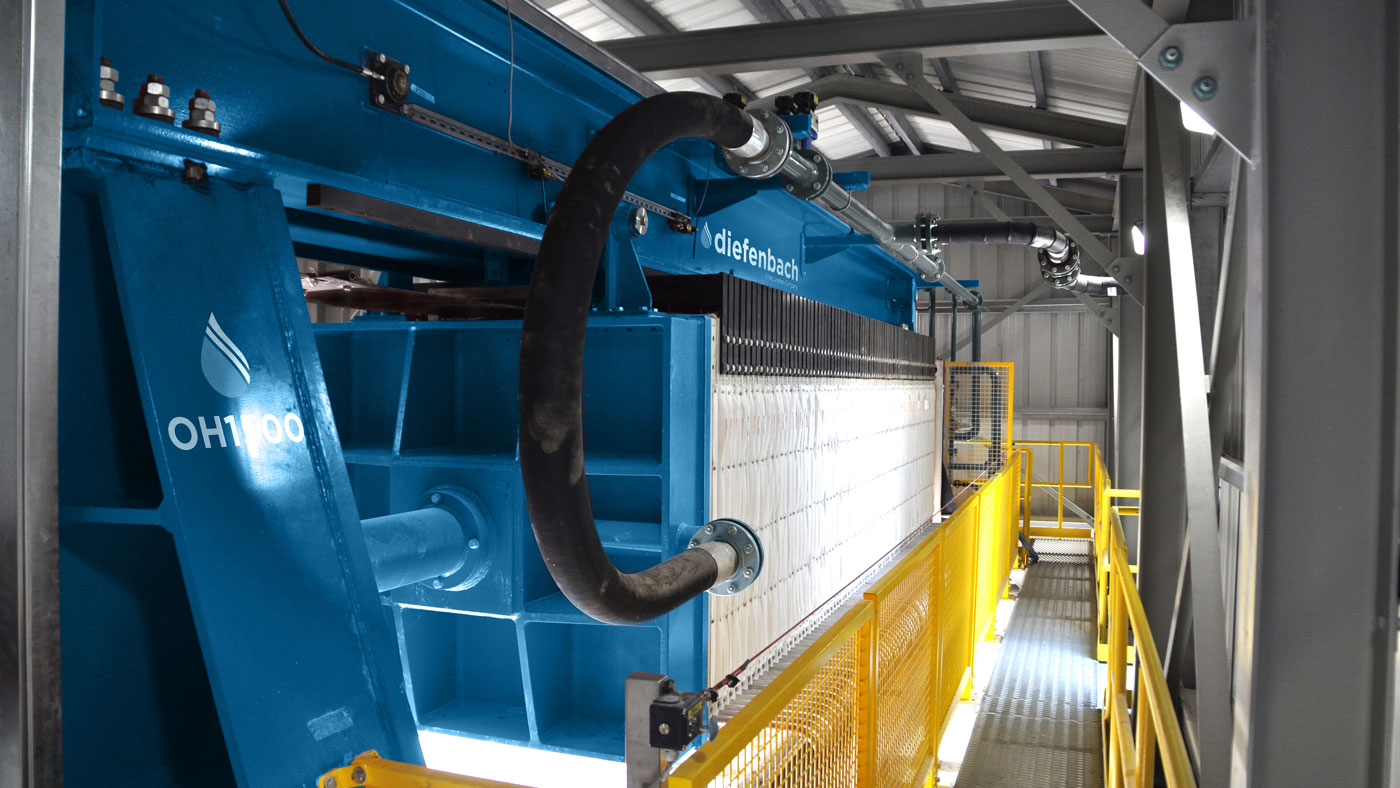
Advanced FEA design with three axes of rigidity
Using advanced Finite Element Analysis (FEA) design techniques and three axes of rigidity, Diefenbach overhead beam filter presses are not subject to torsion of the frame. This is a large structural advantage and has been proven in the field over decades to be a robust and reliable frame design. This design also overcomes the reliability challenges that come from multiple hydraulic cylinders and the complications of keeping these cylinders in sync over time. With only one cylinder on the main drive, the possibility of unexpected structural stresses are reduced.
Additional features
Rapid opening and closing with synchronization guarantee
With only one cylinder on the main drive of Diefenbach overhead beam filter presses, synchronization of the plate movement is guaranteed. Filter presses with 4 cylinders can have issues with maintaining alignment as the filter press opens and closes.
Bidirectional filling via dual feed entry points
Diefenbach overhead beam filter presses feature bidirectional filling, allowing the press to be fed from both sides of the filter press. This cuts the time to fill the filter press in half and reduces the velocity of incoming material to help increase wear life of the filter media. Duel-feed entry also helps improve the consistency of the filter cake from end-to-end vs. presses that are only fed from one side.
Greater access and ease of maintenance
Free space between the plates on Diefenbach overhead beam filter presses is about 800 mm (31”), providing greater access and ease of maintenance. This is roughly 10 times the space available on side-beam presses and allows for easy cloth and plate inspection as well as easy filter cloth changeout.
No side beams to block cake discharge
Because the plates on Diefenbach overhead beam filter presses are not encased between structural side beams, there is no possibility for cake residue to build up on the side of the filter plates as the cakes are discharged. This is a big advantage over side beam filter presses which are prone to cakes rotating and building up against the side beams and eventually preventing good sealing of the filter plates.