CHALLENGE
Inside its chemical-physical plant, Eco R.O.E. has a series of reactors for batch chemical-physical treatment. These are used for separating the water and concentrating the waste.
After further treatment, the concentrated waste requires dewatering to create a product that can be disposed of in a sustainable manner.
The water recovered from this process is further treated and purified. Once thoroughly cleaned and purified, the processed water can be returned to the environment.
“For us, the most important thing is to dehydrate the product as much as possible to be able to recover the water and return it to the environment,” Raspa said. “We need to minimize the amount of waste in the circulation and maximize the recovery of water.”
“By treating different wastewaters from different industries composed by different producers, we have a very wide variability in the production of sludge,” explained Raspa.
To process a wide variety of wastewater types, Eco R.O.E. required a machine with the capability to handle different solutions and still produce consistent results.
SOLUTION
Ultimately, Eco R.O.E. purchased an Overhead Beam Filter Press from Diefenbach to use in the waste management plant.
“After a several-month long study, we found that using a filter press instead of a centrifuge was the best treatment. It allowed us to have a drier sludge that could be better rendered, and the product was more suitable for management as waste,” Raspa explained.
The Diefenbach Overhead Beam Filter Press is a vital part of the wastewater management and treatment process.
At the beginning of each filter cycle, filter plates are closed and held together by a hydraulic mechanism. Each plate is recessed on both sides, forming a series of chambers when held together.
The concentrated waste is pumped into both sides of the filter press at a high pressure, allowing for liquid-solid separation. Water passes through the filter cloths on the plates, while solid waste is collected on the filter cloths as filter cakes.
The water exits the filter press for treatment and the central feed port is further dried to remove residue. The hydraulic mechanism opens each plate, releasing the dewatered waste filter cake.
The Diefenbach Filter Press allows Eco R.O.E. to recover as much water as possible for purification and ultimately returning it to the environment, while also generating a filter cake that is easier to dispose of.
As well as manufacturing quality equipment, Diefenbach provides aid in every step of the sales process to ensure customers receive a fitting solution.
“Thanks to their pre-sales assistance, they helped us size the machine in the most precise and reliable way for our system and treatments,” said Raspa. “We were given the opportunity to see the filter presses being built and operating. Going to see the quality of construction and operation was decisive for us in the selection process.”
The Diefenbach team works to ensure smooth installation and operation of their machines, tailoring every aspect to meet the application.
“The location, the warehouse, all these aspects have made the installation of this machine particularly critical,” Raspa explained. “Thanks to Diefenbach’s support, everything was made much simpler.”
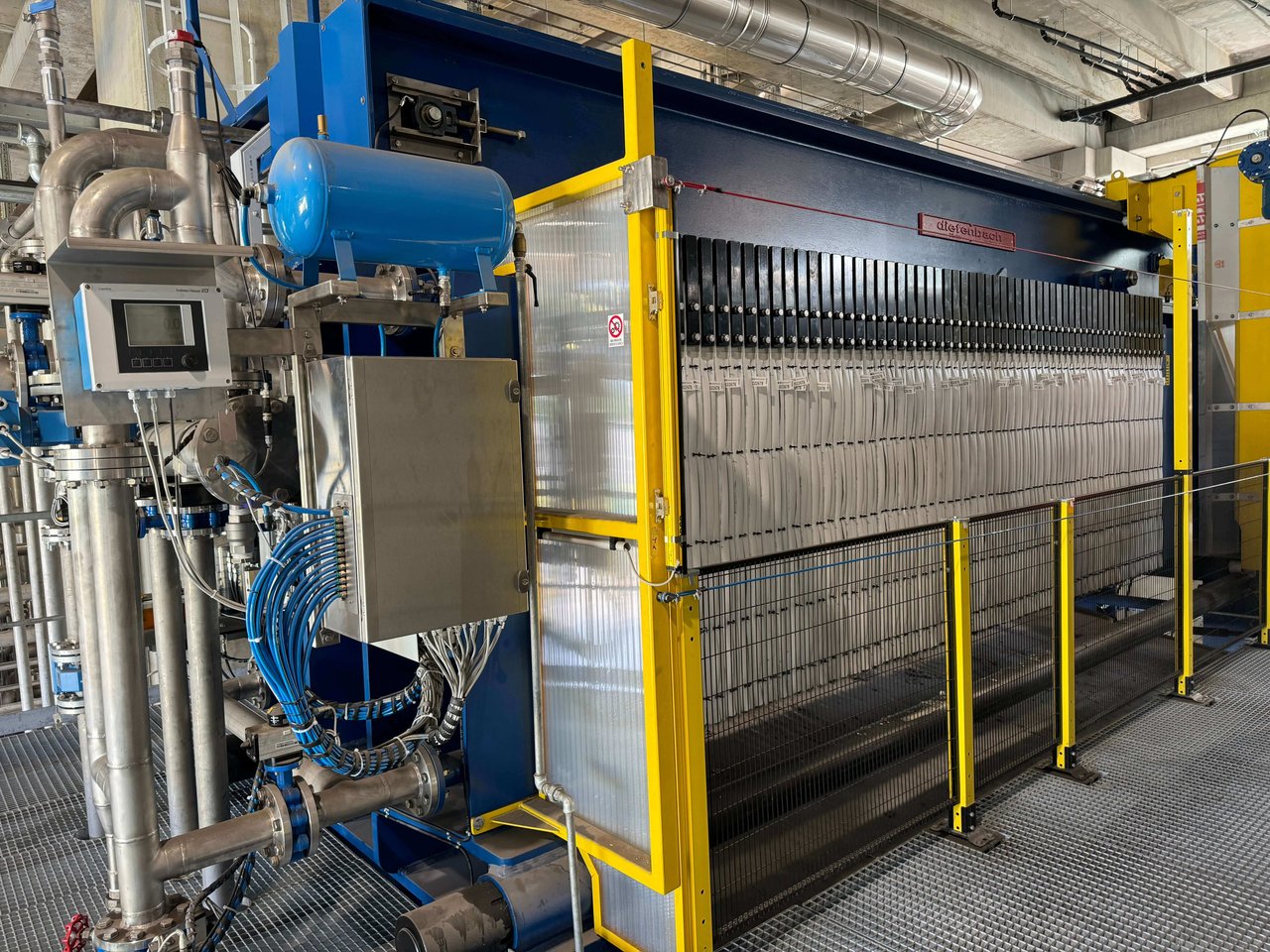
RESULTS
Because Eco R.O.E. processes both non-hazardous and hazardous waste, safety and health are important.
“This filter press has the latest safety features available on the market,” Raspa said. “It is essential for us to try to make the environment in which we work and our surroundings a quiet, peaceful and safe place.”
Tailored features will allow the company to minimize its downtime and get the most out of its new filter press. Ease of maintenance of Diefenbach Filter Presses helps Eco R.O.E. achieve this.
“Maintenance is a fundamental element for us to reduce downtime to a minimum. This machine offers a remote-control system that allows technicians to monitor the machine without stopping it,” Raspa explained. “For us, this a fundamental element to guarantee our customers a constant and quality service.”
Eco R.O.E.’s core mission is to follow sustainable practices to protect the environment while efficiently serving their customers.
“We chose the Diefenbach Filter Press rather than another filtration treatment system because this machinery meets our high standards of effectiveness when processing waste,” said Raspa. “It allows us to significantly reduce the environmental impact of the entire plant and of the customers who use the plant for the treatment of their wastewater.”
The support from Diefenbach’s team was a critical factor for Eco R.O.E. in deciding to use a Diefenbach Filter Press.
“I am very happy to have chosen this brand not only for the quality of the machine, but also for all the support that we have received; from the pre-sales phase up to the assembly and the start-up of this machine,” Raspa said. “Among all the filter presses on the market, we chose Diefenbach because it is synonymous with quality.”