CHALLENGE
Lead-acid battery recycling limits the demand for newly mined lead. In the recycling process, about 97% of the lead-acid battery is recycled.
“Lead recycling is important to the circular economy. The majority of lead produced in the world is from recycling,” said Pizzocri.
An integral part of the lead-acid battery recycling process is filtration and dewatering the desulfurized paste that is produced from crushing the batteries. Because the next step of the process is smelting, the desulfurized paste needs to be as dry as possible.
“The process of dismantling the batteries is a wet process, requiring dewatering to produce a solid cake with the minimum possible residual humidity,” Pizzocri explained.
“Filter presses are the simplest, most cost-effective option for filtration of the paste,” explained Marco Giroletti, project manager office director. “There are other filtration systems that have a poor impact on the environment.”
SOLUTION
Engitec used its first Diefenbach Filter Press in 1979, beginning a partnership that continues to this day.
“The first wet plant was designed for internal use, when Engitec was originally a smelter. We had the problem of dewatering the lead compound slurries,” said Pizzocri. “The solution came when we met the Diefenbach team.”
The lead-acid battery recycling process is composed of three main parts – crushing and separation, paste desulphurization and sodium/ammonium sulphate production, and smelting-refining and gas filtration.
Dewatering is an important step in the lead-acid battery recycling process, specifically the paste desulphurization portion of the process. Before the lead paste can be smelted for further processing, it must be as dry as possible.
Diefenbach Filter Presses create filter cakes with the ideal moisture content for subsequent smelting. The Filter Presses also create a filtrate that can be used to produce another byproduct, sulphate salt, allowing total reuse of material processed through the Filter Press.
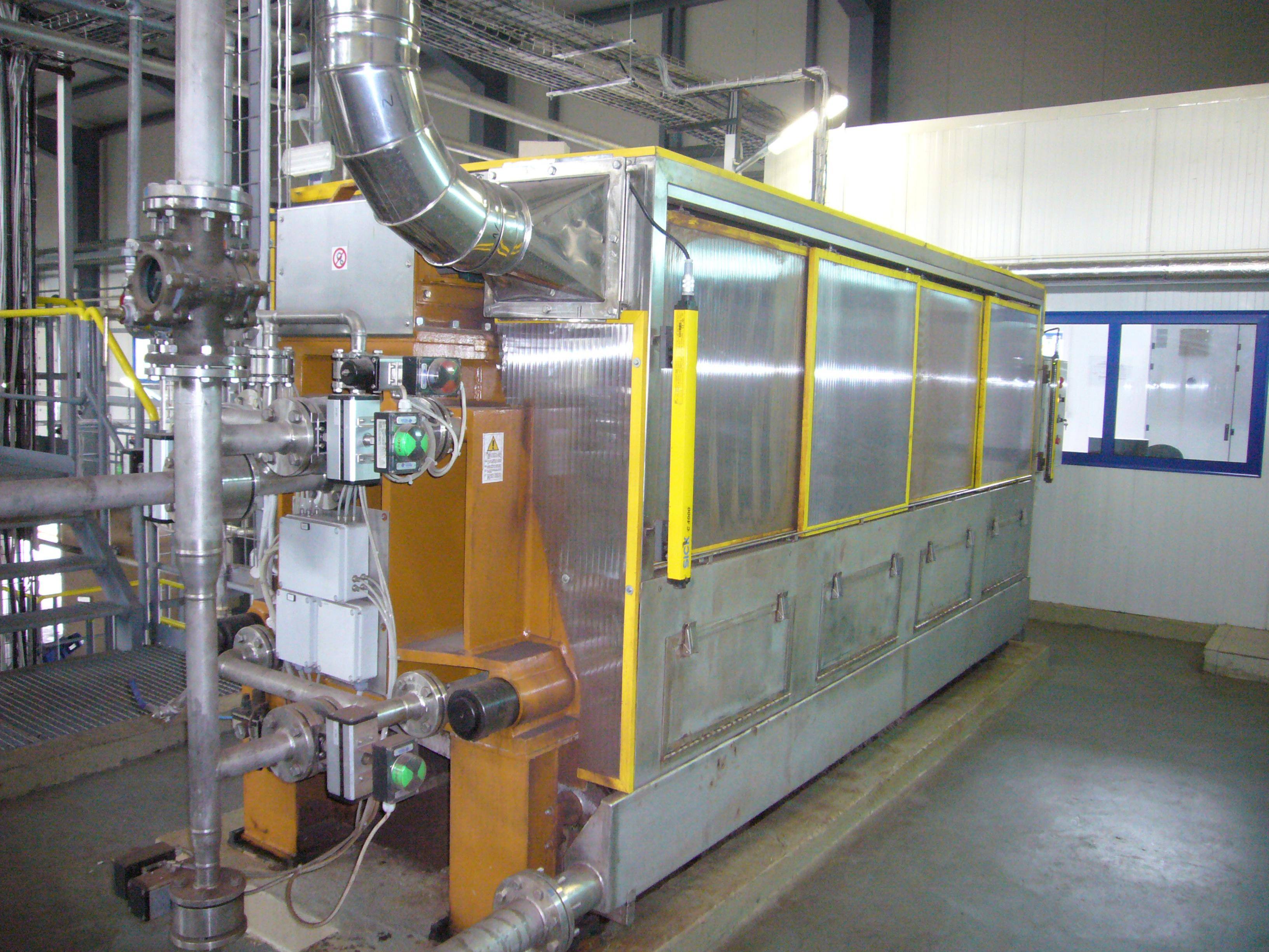
RESULTS
Engitec and Diefenbach have worked together for over 40 years. Diefenbach’s service, support and quality of machinery have provided Engitec with the solution to the dewatering stage of its plants.
Going through some reference numbers, out of the 80 plants Engitec has installed around the world, 70 of them feature Diefenbach Filter Presses.
“The majority of presses in our plants are Diefenbach,” said Pizzocri.
Diefenbach assists Engitec through every stage of the sales process.
“We work with the Diefenbach engineering team starting from the request for quotation, then we work together for the implementation of the control system and up to the testing,” Giroletti said. “There is a good technical team at Diefenbach that we can rely on.”
Because Diefenbach and Engitec have a long history, “When we select the size of the press, we use the past history with Diefenbach to decide which filter press is the best for the capacity of a plant,” Pizzocri explained.
The length of the partnership proves the quality and durability of Diefenbach equipment.
Pizzocri said, “The machines are robust. We have always seen a long duration of operation. The machines are well manufactured.”
Another advantage of Diefenbach Filter Presses is low maintenance.
“There is no big maintenance, no big refurbishment. Some machines have been working for 20-30 years,” said Pizzocri.
Not only do Diefenbach Filter Presses have a long operational life and low maintenance requirements, but they also produce a low moisture content level for the smelting process.
Giroletti explained, “The lead oxide and lead sulphate that comes from crushing the batteries is pumped from a reactor to the filter press, before or after desulfurization, to get a dry cake that can be sent to smelting. It will have a moisture content ranging from 8-12% when entering the furnaces.”
Diefenbach’s knowledge and experience gives Engitec the best solutions for dewatering in its lead-acid battery plants.
Pizzocri said, “The best advantage of working with Diefenbach is that they know what Engitec wants.”